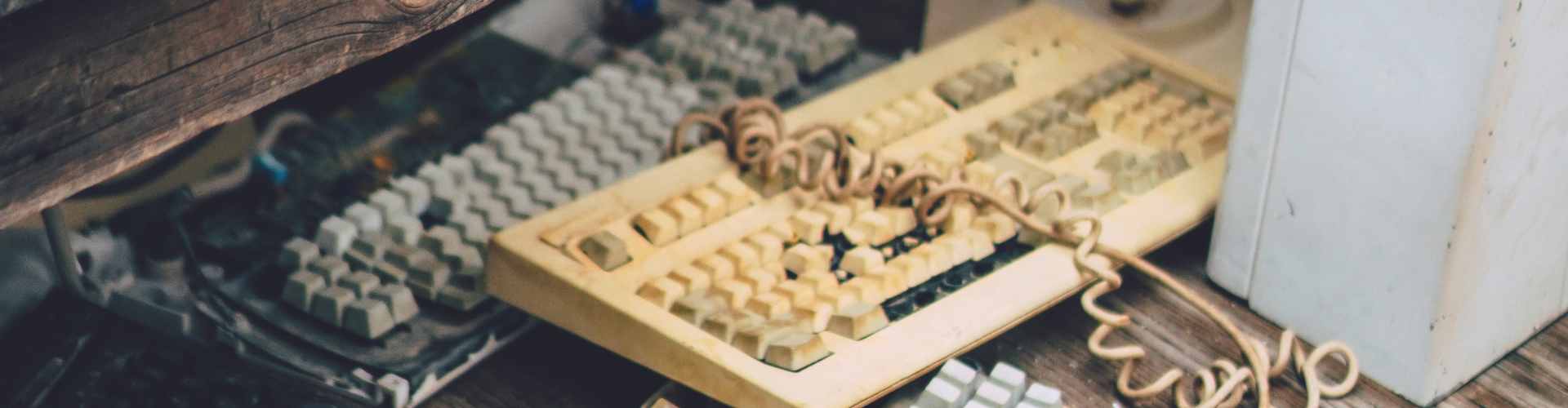
Recycler les déchets : entre redécouvertes fondamentales et nouvelle épopée industrielle
Le décalage entre la rapidité de l’invention technique de solutions de valorisation et la lenteur de l’adoption majoritaire de nouveaux usages de tri amène à revenir aux racines historiques du recyclage. D’une part, l’économie circulaire d’aujourd’hui n’a rien à voir avec celle des sociétés organiques sans déchets, car la valorisation actuelle repose entièrement sur la production d’un déchet, c’est-à-dire d’un rebut détaché de la personne qui l’a produit et ne veut plus le voir. De ce fait, il faut resensibiliser des usagers devenus insensibles à cette part invisible d’eux-mêmes, alors qu’il serait plus efficace d’œuvrer en amont pour que personne puisse dire : « Ceci n’est plus moi. » La comparaison internationale montre que la valorisation des déchets peut être, paradoxalement, plus facile à mettre en œuvre dans les pays émergents où les ordures n’ont jamais cessé d’être des ressources pour les populations vivant autour et sur les décharges.
D’autre part, il ne faut pas oublier que la transposition dans le domaine de l’expertise industrielle et judiciaire de la chimie organique d’Antoine Lavoisier et de Jean-Antoine Chaptal a produit cette idée qu’un déchet n’est rien d’autre qu’un résidu en attente d’être valorisé chimiquement. Cela a neutralisé toutes les luttes contre les pollutions au xixe siècle. L’essor du nouveau marché du recyclage suppose aujourd’hui un contrat de confiance qui lève les ambiguïtés et invente un nouveau métabolisme qui ne peut être la réactivation d’un passé idéalisé.
Grégory Quenet
Le recyclage, au sens moderne du terme, apparaît progressivement au xxe siècle, et surtout à partir de la seconde moitié du siècle. En Grande-Bretagne, le verbe « to recycle » existe depuis 1926, puis on le retrouve décliné en « recycling » juste après la Seconde Guerre mondiale. En France, le terme « recyclage » apparaît quant à lui en 1960, mais dans les deux pays, il faut attendre les années 1970 pour que ces mots soient véritablement employés dans le langage courant, en pleine explosion de la production de déchets. En 1970, le graphiste Gary Anderson crée d’ailleurs le fameux logo universel du recyclage à partir du ruban de Möbius – dont les deux faces ne font qu’une – dans le cadre d’un concours lancé en marge du premier Jour de la Terre, célébré dans le Wisconsin. À l’origine destiné aux produits en papier recyclé, le pictogramme va ensuite se généraliser à tous les produits recyclés ou recyclables dans le monde. S’il n’est accompagné d’aucune mention, il signifie que le produit est simplement recyclable, tandis que l’apparition d’un pourcentage veut dire qu’il contient des matériaux recyclés. Clé de son succès, sa simplicité graphique va permettre de l’adapter à tous les contextes et à tous les pays, à tel point que Gary Anderson réalise l’importance de son design quand il l’aperçoit sur une poubelle à Amsterdam quelques années plus tard !
Héritiers des anciens chiffonniers, les premiers à recycler la matière issue des déchets après 1945 sont les cartonniers, les papetiers et les verriers. À cette époque, les Établissements Soulier, qui intègreront la CGEA et Veolia, abandonnent leurs activités de chiffonnerie désormais déclinantes pour s’orienter vers le recyclage du papier en s’associant avec les Cartonneries La Rochette. Pour alimenter ses usines, l’entreprise Soulier récupère les papiers des centres commerciaux, des supermarchés et même dans les écoles après avoir sensibilisé les écoliers à cette collecte. Après le choc pétrolier de 1973, les verriers incitent les Français à recycler leurs bouteilles en verre, car le verre recyclé réclame moins d’énergie. C’est la première fois qu’une telle filière est mise en place à partir des déchets ménagers. En 1976, une convention de l’industrie verrière – représentée par la Chambre syndicale des verreries mécaniques de France – est signée avec le ministère de l’Industrie et de la Recherche.
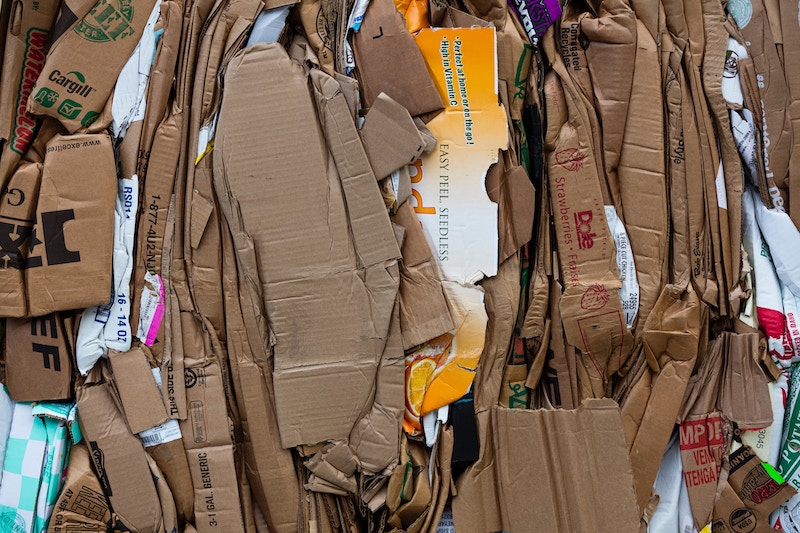
Mais ces initiatives occupent une place encore bien maigre à côté de l’explosion de ce qu’un reportage télé de 1972 appelle « les emballages perdus » 1, à savoir non consignés. Ces derniers représentent 5 % des emballages en 1960, 30 % en 1972, et le journaliste évoque des prévisions de 80 % en 1980. De 220 kilogrammes de déchets produits par an et par habitant dans les années 1960, la France passe à 360 kilogrammes en 1990. Face à cette tendance, il n’existe pendant longtemps que des efforts localisés de recyclage. C’est à partir des années 1980 que les choses changent d’échelle, de façon très pragmatique. « On a alors été en mesure de mettre en place des filières, fait remarquer Martial Gabillard, directeur de la valorisation des flux chez Veolia. On identifiait des gisements, du bois de recyclage, des plâtres, même du plastique. Notre activité Propreté a été amenée à proposer de plus en plus de tri. Si on voyait qu’il y avait du bois dans la région, alors on faisait une benne pour ça. Dans les déchetteries, on installait des bacs pour les déchets verts, parfois si besoin pour du carton, de la ferraille, ça servait aux cartonniers, aux ferrailleurs. Mais il a fallu attendre la loi de 1992 pour orchestrer ces flux. »
Reflet de son temps et de ce que d’autres pays engagent en même temps, la loi Royal rénove la politique française de gestion des déchets ménagers : en plus d’inciter à la réduction de l’enfouissement et à la production d’énergie à partir de l’incinération, elle préconise la réduction de la production de déchets et leur valorisation, poussant pour cela au développement de nouveaux types d’équipement tels les centres de tri et des déchetteries. Comme en Allemagne dès 1989, elle va étendre davantage la responsabilité élargie du producteur, définie avec le principe pollueur-payeur par la directive européenne de 1975, aux déchets ménagers, et développer les éco-organismes, fédération de producteurs rassemblés pour assurer cette responsabilité sur la fin de vie de leurs produits.
« Dans les années 1990, les collectivités n’ont plus les moyens financiers et techniques pour gérer les déchets, qui se complexifient, indique Helen Micheaux, maîtresse de conférences en sciences de gestion à AgroParisTech. Il faut trouver une autre solution. C’est dans ce contexte que va émerger la réflexion de responsabiliser le producteur. » « Il y a eu une vraie prise de conscience. Tous ces déchets que l’on maniait, on pouvait les recycler. Pour cela, il fallait les sortir de la poubelle ménagère en mettant en place des filières spécifiques de recyclage afin de les trier, puis les préparer pour les réincorporer, explique Françoise Weber, directrice des schémas REP en France chez Veolia. Avec les éco-organismes, on commence à trier les emballages en plastique, en carton, en papier, en verre. » En ce début des années 1990, le temps est venu de donner un coup d’accélérateur au recyclage.
Le plastique n’est plus fantastique, et surtout plus à sens unique
Le plastique, il faut le dire, a pris une place centrale dans le monde des emballages et des déchets. Indépendamment des chocs pétroliers, les déchets en plastique sont passés de 4 % des déchets ménagers en France en 1973 à 11,2 % cinquante ans après. La recherche de la simplicité et de la facilité a dominé une époque en attente d’une libération totale des contraintes physiques, alors que dès le départ, tout était en germe. En 1972, dans le reportage télé diffusé et archivé par l’INA, le directeur d’une société d’emballage plastique vantait les mérites de son activité : « On a toujours jeté les emballages, rappelez-vous les boîtes de conserve, les bidons… [...] La tendance normale est de chercher des emballages légers, qui ne soient pas consignés, et les matières plastiques sont idéales pour cela. » 2
Le plastique était fantastique, au point qu’un artiste belge s’en fasse un nom de scène : ça plane alors pour Plastic Bertrand, qui fait dans son patronyme référence au plastique dont sont faits les habits des punks, un mouvement qui revendique la rupture d’avec la génération qui le précède. Dans le même temps, en aval du système de production et de consommation, le directeur d’une usine d’incinération, un certain M. Fourment, commençait pourtant à déplorer la multiplication des bouteilles en plastique dans les déchets : « Ces bouteilles sont indestructibles, c’est pour ça que dans une certaine mesure, quand on parle de biodégradabilité, pour nous, dans l’état actuel de nos connaissances, c’est de la science-fiction. » 3
Jean Soulier, chantre de la récupération des déchets et patron social
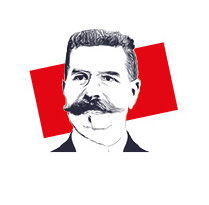
Né en 1868 à Meulan-en-Yvelines, Jean Soulier a connu un parcours dont les épisodes épousent les contingences historiques de la première moitié du xxe siècle. Après ses études au lycée Lakanal à Paris, il intègre l’entreprise familiale de récupération et valorisation de déchets pour se former, mais son mariage avec Emma Vachon le conduira à Rouen pour travailler avec son beau-père. C’est dans cette ville qu’une grande partie de l’activité de recyclage de papiers et de textiles des Établissements Soulier, maîtres-chiffonniers, va prospérer de façon industrielle, même si l’entreprise reste à taille humaine.
Dans les années 1910, Jean part aux États-Unis et en Russie – de quoi se créer un carnet d’adresses dans l’exportation qui lui servira toute sa vie ! Contrairement aux entreprises de ramassage des déchets qui gèrent un service public, les Soulier vivent directement de leur commerce : ils achètent des déchets, trient, valorisent et revendent plus cher, bref, ils gagnent de l’argent grâce aux marges qu’ils dégagent de cette mission. De fait, ils dépendent de l’offre et de la demande des produits, et ne s’installent dans une région que s’ils estiment qu’il existe un débouché.
Dans ce contexte, la guerre de 1914-1918 met un coup d’arrêt provisoire à leur développement : dans l’Aisne, par exemple, une usine est détruite. En 1919, la famille décide d'organiser autrement l’entreprise, qui se recentre à Rouen et se transforme en Société anonyme des anciens établissements Soulier. Chaque frère se concentre sur une activité : Jean est négociant de chiffons en gros et Eugène négociant en commerce de peaux, cuirs et cornes. En tant que troisième administrateur, Georges, le fils de Jean, s’occupe de la récupération et de l’effilochage de chiffons et rognures pour les papeteries. Leurs magasins commencent à ouvrir partout dans la ville et aux alentours. Un grand entrepôt voit le jour. Et ce n’est pas tout : la famille achète des biens immobiliers pour loger les ouvriers qui viennent travailler, parfois de façon saisonnière, dans leurs usines.
Les années 1920 représentent l’âge d’or des Établissements Soulier. Grâce à leur croissance, ils peuvent acheter un grand terrain à la plaine Saint-Denis, une zone où beaucoup de chiffonniers de gros sont déjà implantés. Ils y installent une succursale à partir de laquelle ils vont pouvoir se développer aussi à Paris pour les peaux et les cuirs, qu’ils revendent aux fabricants de chaussures de la capitale et de sa banlieue. Suit alors l’achat d’un fonds de commerce parisien et d’ateliers à Montreuil pour la branche peaux.
À cette époque, les Soulier dépassent toutes les autres installations de chiffons à Paris, si bien qu’ils entrent en Bourse en 1924. Certes, l’activité de chiffonnier connaît des complications dans les grandes villes depuis l’arrivée du camion poubelle, qui passe tous les matins très tôt, mais dans les petites villes et villages, il est toujours possible de faire de la collecte auprès des particuliers, bien contents de revendre leurs chiffons, leurs peaux de lapin, leurs restes d’os animaux, ou de fouiller les décharges sauvages. Notable de la ville et membre du conseil général depuis 1901, Jean Soulier reste malgré tout fidèle à Rouen, même s’il habite une partie de l’année au 115 boulevard Haussmann à Paris. Radical-socialiste, il œuvre également pour améliorer les conditions de travail des métiers de la récupération et du tri. Il fait construire des logements pour les ouvriers saisonniers de ses usines, développe l’apprentissage, fonde la caisse de secours mutuel de la profession et tente de maintenir une production toute l’année pour « éviter du chômage au personnel ». En 1921-1923, il ordonne la modernisation des anciens établissements de la plaine Saint-Denis, avec réfectoire, vestiaires, lavabos et douches pour les ouvrières !
Avant le krach de 1929, Jean Soulier refait une tournée aux États-Unis, toujours dans l’optique de développer ses exportations. Mais la crise économique mondiale va vite le faire déchanter.
En juin 1930, Jean Soulier avoue que « c’est un véritable arrêt auquel il faut faire face » – l’entreprise passant de 25 000 tonnes de marchandises à 16 544 tonnes. L’établissement se tourne vers la vente de biens immobiliers pour survivre. Malgré ses aspirations sociales, Jean Soulier peine à appliquer les lois sociales du Front populaire en 1936, notamment les congés payés et la semaine de quarante heures qui fragilisent un modèle économique déjà vacillant. Pendant la Seconde Guerre mondiale, le chef de famille perd des proches collaborateurs, parmi lesquels son propre fils Georges. Ses ateliers sont bombardés à Rouen. Les Établissements Soulier s’associent avec les Cartonneries de la Rochette pour créer la Société nouvelle des établissements Soulier en 1946, une dernière tentative de sortir de la crise de la récupération des chiffons, des papiers et des peaux, mais les chiffres ne décollent toujours pas. Malade, Jean Soulier délègue une partie de ses fonctions et décède en 1954, à Rouen, où son entreprise continue de récolter les chiffons comme elle peut et de les exporter. Les Établissements qui portent son nom seront absorbés par le groupe papetier des Cartonneries de la Rochette en 1960, lequel à son tour les revendra à la Compagnie Générale des Eaux en 1990, alors qu’elle consolide différentes activités pour constituer des services complets de gestion des déchets. Si cette activité de recyclage reste fragile, elle permettra au groupe de développer ses expertises en la matière.
À Chennai, le secteur informel, maillon clé du recyclage
Véritable puissance démographique avec 1,4 milliard d’habitants, la population de l’Inde supplante désormais celle de la Chine. Si l’on ajoute à cela une urbanisation galopante et un accès grandissant à la consommation de masse, le sous-continent fait face à des défis majeurs en matière de gestion des déchets. Historiquement, il y a toujours eu ceux qu’on appelle les « récupérateurs informels » et ils y jouent encore un rôle crucial, qui nécessite d’être pris en compte par les grandes entreprises comme Veolia.
Les villes indiennes produisent 68,8 millions de tonnes de déchets par an, une quantité qui pourrait augmenter de 133 % entre 2015 et 2041, chiffre qui donne le vertige, d’autant plus que 91 % des déchets collectés ne sont pas valorisés et terminent leur vie dans des décharges à ciel ouvert.
En Inde, les déchets post-consommation sont cependant parfois pris en charge par le secteur informel, des hommes et des femmes qui proposent un service de pré-collecte et de valorisation. Selon un document du réseau Centraider « ces opérateurs sont souvent difficiles à connaître et à identifier, car ils se rendent peu visibles pour éviter les humiliations par la population ou des redressements par les autorités ».
C’est pourquoi les collectivités ou même les entreprises ont du mal à collaborer avec les travailleurs et travailleuses du secteur informel. Pourtant, les enjeux sont importants, comme le rappelle Kabadiwalla Connect, une entreprise sociale de technologie basée à Chennai : « Tirer parti de l’écosystème informel des recycleurs de déchets urbains permettrait de réduire de 70 % la quantité de déchets envoyés en décharge dans les villes indiennes. »
Chiffonniers, recycleurs, récupérateurs, travaillent souvent dans des conditions précaires, mais ils jouent un rôle essentiel dans la gestion des déchets, contribuant à réduire la quantité de déchets mais aussi à minimiser leur impact environnemental. En 2015, dans la ville de Chennai, Kabadiwalla Connect a cartographié et recensé pour la première fois les « récupérateurs-entrepreneurs » de déchets, appelés « kabadiwalla » en Inde. L’étude en a identifié près de 2 000 rien qu’à Chennai, où ils collectent plus de 24 % du total des déchets recyclables : le papier, le métal, le plastique et le verre.
Néanmoins, ces acteurs rencontrent divers problèmes : manque de visibilité, informations lacunaires et absence d'intégration officielle dans le système. Pour les pallier, Kabadiwalla Connect a développé une plateforme visant à faire interagir les entreprises telles que Veolia et le secteur informel. « Notre objectif est ici de renforcer la valeur de la chaîne d’approvisionnement informelle, explique Siddharth Hande, le fondateur et PDG de Kabadiwalla Connect. L’une de nos principales initiatives est la mise en place d'une installation de récupération de plastique très optimisée, approvisionnée par le secteur informel. Nous avons un an et demi d’expérience sur le PET (plastique pétrosourcé, ndlr) et nous avons un niveau de qualité élevé : 80 à 90 % de PET récupéré en moyenne, grâce à un bon tri. Le partenariat avec Veolia nous aide à améliorer la transformation et la valorisation haut de gamme. »
L’entreprise a mis en place une infrastructure de recyclage spécifique pour obtenir des matériaux recyclables provenant du secteur informel, en se concentrant initialement sur le plastique. L’objectif est de démontrer qu’il est possible d’obtenir un volume important de déchets provenant du secteur informel tout en bénéficiant de meilleurs prix, d’un meilleur horaire de collecte et d’une meilleure connaissance du marché du recyclage.
Progressivement, l’importance de maîtriser les impacts environnementaux de ce nouveau matériau émerge. C’est en Allemagne et dans les pays scandinaves que, pour y parvenir, le tri sélectif s’impose le plus vite dans la population. Marc-Olivier Houel, directeur général de l’activité Recyclage et Valorisation des déchets en France mais aussi ancien responsable déchet industriel et ordures ménagères en Sarre, se souvient bien de cette période où tout était à inventer : « Les Allemands ont été précurseurs sur les éco-emballages et la création des éco-organismes, raconte-t-il. C’est en septembre 1990 qu’ils mettent en place le premier éco-organisme en Europe – le DSD (Duales System Deutschland) – et le Point vert (Der Grüne Punkt) – ce logo circulaire représentant deux flèches enroulées qui signale que l’entreprise contribue au traitement des emballages, qui sera ensuite repris dans de nombreux pays, dont la France.
Veolia, qui vient de prendre pied en Allemagne à travers le rachat de la société transfrontalière Kléber, va jouer un rôle d’accompagnement central, en conseillant les villes sur l’application de la nouvelle réglementation, en distribuant de nouveaux sacs jaunes transparents, en assurant la sensibilisation des citoyens par l’intermédiaire des opérateurs de collecte et par le recrutement spécifique d’ambassadeurs de tri. » Petit à petit, les déchets comme les bouteilles et les films plastiques, mais aussi les pots de yaourt, les emballages Tetra Pak, les canettes d’aluminium... sont collectés pour être redonnés au DSD : sur le territoire du Land de Sarre, les quantités des emballages ménagers légers collectés et triés passent de 0 en 1992, date de mise en service du premier système de collecte sélective, à 30 kilogrammes par habitant et par an en 1995.
Mais, pour tout dire, en Allemagne même, trier n’a pas immédiatement suffi à recycler. Les flux de plastique créés n’ont pas tout de suite trouvé de débouchés, qui ne préexistaient pas : ils ont en revanche conduit à les engendrer, à partir de la fin des années 1990. « C’était comme une startup, se rappelle Marc-Olivier Houel. On était en train de transformer notre environnement, et celui de nos clients, en mettant la pression sur le réemploi des matières. » La création d’un gisement de matière permet, cinq à six ans plus tard, de créer des filières dédiées de recyclage des plastiques dans des pots horticoles ou dans l’industrie automobile. En 1998, Mercedes signe un contrat-cadre pour la collecte chez les concessionnaires et le recyclage des pièces endommagées (pare-chocs, verre, batteries, essuie-glaces…). « On a trouvé des filières de revalorisation avec Mercedes dans toute l’Europe, se souvient Marc-Olivier Houel. Le système fonctionnait quasiment en boucle fermée. On a ainsi été moteur pour promouvoir l’élan de l’économie circulaire en Allemagne et en Europe. »
Pour multiplier les filières, les partenariats avec de grandes entreprises s’imposent comme un moyen d’explorer les possibles et de trouver des débouchés nouveaux au plastique recyclé, historiquement plutôt utilisé pour des applications peu techniques, du type tuyaux en PVC recyclé. Cela implique à la fois d’ « accompagner les industriels à changer leur approche sur la matière première, explique Martial Gabillard, de leur faire accepter les petits défauts dans le plastique recyclé ». Mais aussi, pour Veolia, de s’adapter aux demandes les plus complexes d’entreprises soucieuses de conserver des produits de qualité, aux spécificités techniques précises. Depuis plus de vingt ans désormais, les progrès ont été considérables, jusqu’à ce qu’en 2021 le leader technologique Thalès s’associe à Veolia pour créer la première carte SIM écoconçue à partir de plastique recyclé, capable de remplir les conditions de solidité, de souplesse, de résistance aux contraintes de chaleur indispensables au produit.
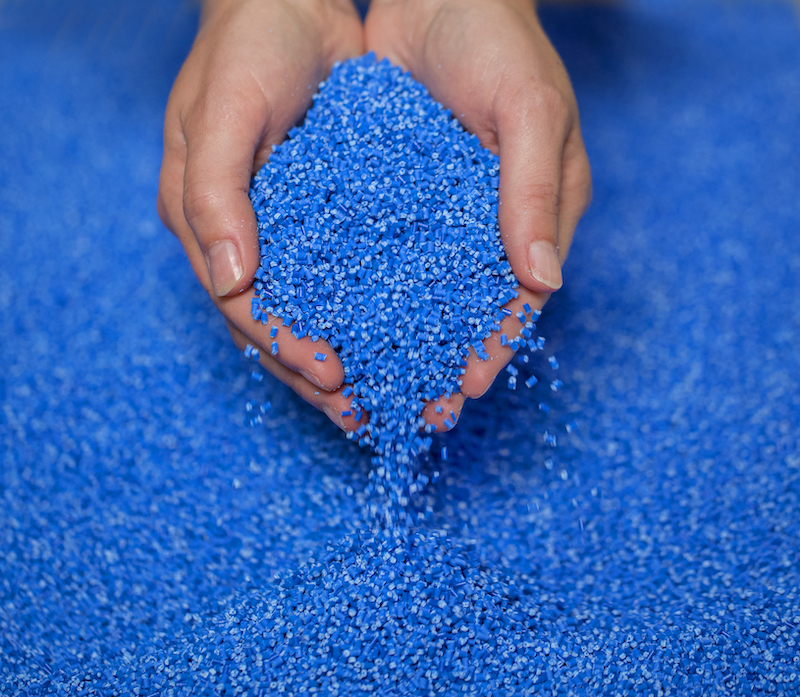
© Médiathèque Veolia - Christophe Majani D’Inguimbert
Plus globalement, « il y a un grand travail de partenariat avec les éco-organismes. Il faut travailler ensemble pour mobiliser à long terme des gisements qui alimentent les unités industrielles, elles-mêmes novatrices dans les métiers du recyclage », considèrent ensemble Françoise Weber et Sophie Petibon, directrice commerciale de l’activité Recyclage et Valorisation des déchets chez Veolia. Un travail partenarial qui porte aussi sur l’écoconception, pour permettre de boucler les boucles. Veolia encourage notamment ses partenaires à fabriquer des produits monoplastiques, plus épurés et simples, dont le recyclage nécessite moins de produits chimiques et d’énergie. « Nous avons une offre pour les industriels de conseil sur l’écoconception et de certification du niveau de recyclabilité de leurs emballages, explique Sven Saura, directeur du pôle Recyclage et Plastiques de Veolia. Il faut savoir qu’on émet 75 % de CO2 de moins avec une bouteille en plastique recyclé par rapport au plastique vierge, et que l’écodesign peut encore réduire cette portion. »
Simplifier et standardiser les matériaux plastiques utilisés, et en particulier ceux issus du recyclage, est clé pour favoriser le développement de l’économie circulaire. C’est la raison pour laquelle Veolia a formalisé en 2022 sa marque de polymères circulaires PlastiLoop. Avec elle, le groupe propose une gamme de produits recyclés structurée pour répondre aux besoins des différents industriels qui souhaitent se passer de plastique vierge, une offre adaptée aux besoins de chaque industrie, de l’automobile à l’agroalimentaire, afin d’aller enfin vers un monde où le recyclage devient un standard partagé.
Reste que nous sommes encore loin d’avoir résolu l’enjeu de l’usage et du recyclage du plastique. Le monde consomme chaque année plus de 350 millions de tonnes de plastiques et, d’après les prévisions du Programme des Nations unies pour l’environnement, si rien n’est fait, le chiffre de la consommation pourrait avoir triplé en 2060 et dépasser le milliard4 ! Dans le monde, seuls 9 % du plastique sont recyclés, presque 50 % sont mis en décharge, 19 % sont incinérés, et le reste vient polluer l’environnement, parfois sous forme de micro- ou nanoplastiques : « Chaque minute, l’équivalent d’un camion-poubelle rempli de déchets plastiques se déverse dans les océans » 5, peut-on lire dans un article du Monde publié en 2023. Alors que les solutions techniques se développent, la réglementation aura encore un rôle à jouer, dans le même pas de deux souvent constaté entre la technique et la loi. Les obligations de réincorporation de plastique recyclé dans les produits, à l’image de l’obligation faite par l’Union européenne aux embouteilleurs d’incorporer au moins 25 % de plastique recyclé en 2025 et 30 % en 2030, seront déterminantes.
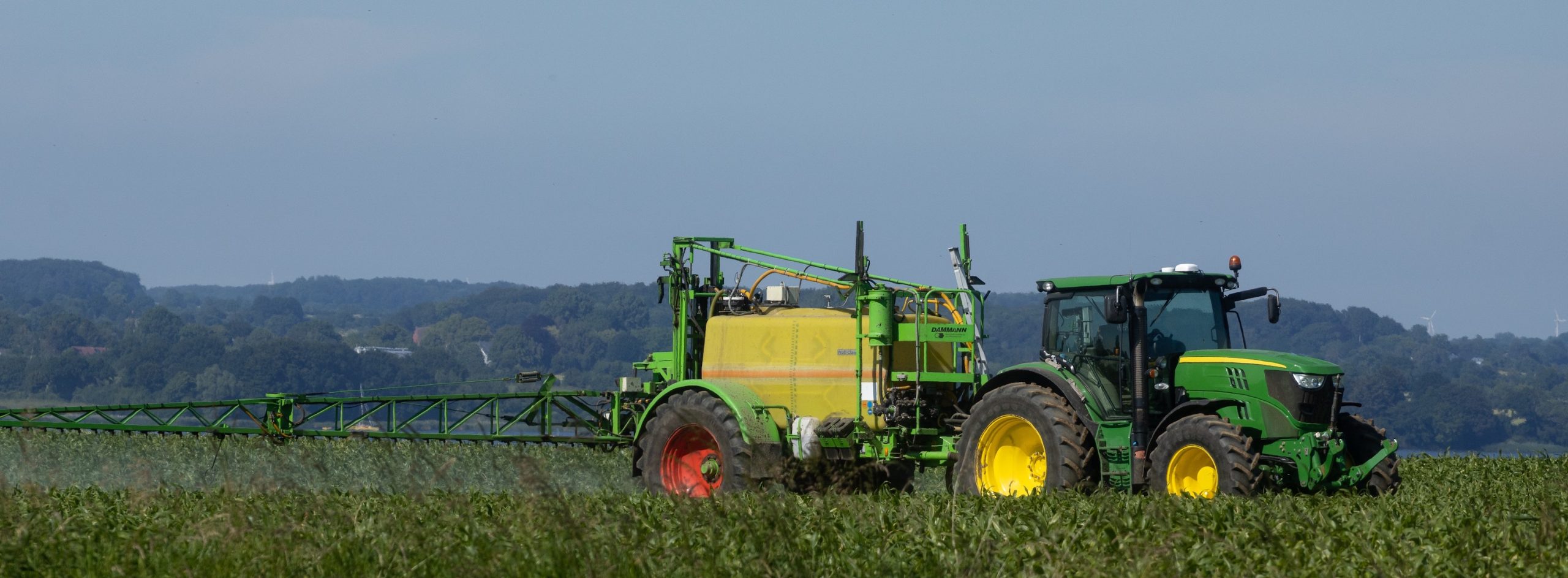
La valorisation organique : des engrais agricoles à la nutrition animale
Les matières organiques sont historiquement parmi les déchets les mieux valorisés, avant l’apparition des villes sanitaires. Tirés des boues urbaines et vidanges issues des fosses d’aisances, ils étaient transformés via des procédés industriels en engrais ou en compost, avant la création des réseaux d’égouts, qui rendent ces boues trop liquides pour être épandues dans les champs, et l’évacuation en masse des ordures ménagères, peu à peu mélangées mais aussi compactées et tassées dans les bennes à ordures, rendant presque impossible leur valorisation.
Le retour en grâce des engrais organiques
Le XXe puis le XXIe siècles, au gré de l’émergence des stations d’épuration et de la nouvelle distinction des flux, vont réinvestir, avec plus de précision, le recyclage de la matière organique, comme en 1926 à Milwaukee. Veolia mobilise en ce sens ses boues d’épuration, et met en place, au fil de l’évolution des réglementations et des besoins, une logistique qui permet aujourd’hui d’opérer ce retour à la terre. Collectés directement auprès des acteurs de l’industrie agroalimentaire, de la grande distribution ou de la restauration, les déchets biodégradables sont acheminés vers des unités de compostage avant d’être épandus dans les champs. Le compostage constitue la méthode clé de valorisation de ces déchets. Il s’agit d’un processus biologique contrôlé de dégradation des matières organiques, telles que les déchets alimentaires, les résidus de jardin et les sous-produits agricoles. La technique, ancienne, permet de transformer ces déchets en compost, un amendement organique riche en nutriments, qui peut être utilisé comme engrais pour fertiliser les sols agricoles mais aussi les jardins des particuliers. Veolia a travaillé à optimiser ces processus, et surtout à les opérer dans les conditions sanitaires et environnementales strictes définies par une série de lois et de directives qui ont pris en compte la diversité des pollutions à traiter avant le retour au sol.
Ce retour en grâce de la valorisation organique est plus qu’un retour au bon sens. À l’heure du changement climatique, elle est un moyen de capturer le carbone dans les sols. « Les biodéchets permettent à la fois de nourrir les plantes grâce à des fertilisants riches en azote et en phosphore, et d’enrichir les sols en carbone », souligne Maelenn Poitrenaud, responsable innovation et développement de Sede chez Veolia, l’entité dédiée aux services à l’agriculture en France. D’après l’initiative 4 pour 1 000, engagée par le ministre français de l’Agriculture Stéphane Le Foll à l’occasion de la COP21 à Paris en 2015, une croissance annuelle de 0,4 % des stocks de carbone séquestrés dans le sol permettrait de limiter la concentration du CO2 des activités humaines dans l’atmosphère. Un vrai potentiel en perspective, quand on sait que, rien qu’en France, la seule Sede composte chaque année 800 000 tonnes issues de ses 60 sites de compostage. Sans compter que dans un sol enrichi en nutriments, les plantes se développent plus rapidement, et capturent ainsi plus de carbone par la photosynthèse. D’où l’importance de revenir en masse à la valorisation organique.
En France, la valorisation des biodéchets a pu progresser grâce à une réglementation stricte visant à promouvoir leur tri, leur collecte séparée et leur traitement approprié. Depuis le 1er janvier 2012, les gros producteurs de biodéchets sont dans l’obligation de mettre en place des solutions de tri et de valorisation de ces déchets. Au fil des années, la loi AGEC (Anti-gaspillage pour une économie circulaire) a diminué ce seuil afin qu’en 2024 l’ensemble des producteurs soit concerné par cette obligation. Les collectivités vont dès lors devoir offrir aux particuliers des solutions de collecte séparée et de valorisation, par le biais notamment du compostage individuel et collectif. Le défi est de taille quand on sait qu’aujourd’hui la moitié des biodéchets finit dans la poubelle grise, et que seule 30 % de la population déclare trier ses biodéchets à la source. Les solutions existent, encore faut-il pouvoir les généraliser et leur donner les moyens de se déployer, en France comme partout à travers le monde, pour leur donner toujours plus de valeur.
Le développement de valorisation à plus grande valeur ajoutée
À l’inverse d’une massification indistincte des flux, c’est leur séparation toujours plus fine qui permet d’enrichir la valeur de la matière organique recyclée. Avec Angibaud et Recyfish, Veolia commercialise des fertilisants à base de restes de poisson. Principalement utilisé dans les cultures à haute valeur ajoutée comme la viticulture et le maraîchage, le « guano de poisson » créé est un engrais organique riche en azote et en phosphore, agissant également sur la microfaune et la microflore du sol, précieux pour les bons échanges des éléments entre le sol et la plante.
La montée en gamme passe aussi par la maîtrise de nouvelles techniques. « Depuis sa création en 1979, la Sede a acquis davantage de compétences autour de la boue, du séchage, du compostage, de la méthanisation, bref, de quoi proposer aujourd’hui une offre plus variée sur les voies de valorisation des biodéchets, détaille Morgane Maurin, sa secrétaire générale. Ce qu’on épand dans les champs, c’est une gamme très diverse, du compost haut de gamme, des engrais premium comme Pro-Grow, Vital et ADS. » Sur les sites de compostage de Veolia, relève Guillaume Wallaert, ancien directeur de l’offre biodéchets chez Veolia, « le système AEROcontrol accélère par exemple la dégradation des résidus grâce à une sonde qui mesure les paramètres comme la température du compost pour optimiser l’injection d’air, améliorer le processus de maturation et obtenir un compost de meilleure qualité ».
Pour accompagner au mieux les agriculteurs, Veolia a aussi innové dans l’agriculture de précision. Pendant l’épandage, il est également possible d’observer comment les plantes consomment l’engrais et quels sont leurs besoins, afin d’optimiser son utilisation. « On applique des biostimulants à la plante pour qu’elle utilise au mieux le fertilisant, ce qui va lui permettre de se développer de manière optimale et de résister à son environnement », indique Maelenn Poitrenaud. Idem pour les sols, puisque l’application Soil Advisor aide les agriculteurs à optimiser la fertilisation en utilisant des engrais biologiques, comme le compost.
Veolia va aujourd’hui jusqu’à être actionnaire de Mutatec, une startup qui transforme les biodéchets en protéines destinées à la nutrition animale, grâce à l’élevage de mouches soldats noires, lesquelles fabriquent des concentrés protéiques d’insectes à partir de la matière. « La bioconversion est une activité d’avenir qui répond à un enjeu d’alimentation mondiale et d’objectif d’économie circulaire en offrant une meilleure voie de valorisation aux sous-produits organiques », souligne Jean-Christophe Perot, directeur régional pour la région Sud-Est chez Sede.
De la dépollution à la valorisation : l’exemple emblématique des déchets dangereux
Les progrès du recyclage au cours des dernières décennies se sont faits à la fois par la redécouverte de pratiques anciennes et par la mise en place de responsabilités nouvelles, par le développement de nouvelles techniques et par le renforcement des normes environnementales. Les différents flux de matières ont ainsi connu une amélioration de leur valorisation, mais aucun n’est sans doute aussi emblématique de l’époque et de l’ADN de Veolia que celui des déchets dangereux. Constituant une pollution nouvelle et complexe, ces déchets ont vu leur traitement puis leur recyclage se développer à partir de l’esprit d’entreprise des équipes de Veolia. Cette histoire, Jean-François Nogrette, directeur de la zone France et déchets spéciaux Europe, la connaît bien. « C’est la branche Eau de Veolia qui va inventer ce qui est devenu le traitement du déchet dangereux, pour préserver sa ressource », résume-t-il. Tout commence lorsque Bertrand Gontard, directeur de l’usine de potabilisation de l’eau de Méry-sur-Oise, se rend compte que les effluents industriels rejetés dans l’Oise menacent le traitement de la ressource. Pour potabiliser, il doit utiliser encore plus de charbon actif, et la pénurie guette, ce qui signifierait la coupure d’eau potable pour les habitants. Pour remédier au problème, il propose aux industriels de traiter directement leurs effluents dans un centre spécialisé et sans attendre que le rejet pollue la rivière.
« Dans sa carrière, il a aussi connu une société qui s’appelle la SARP, reprend Jean-François Nogrette, et qui faisait ponctuellement de la collecte et du pompage de déchets dangereux. Il s’en inspire pour créer la SARP Industries en 1975, une filiale de la Compagnie Générale des Eaux », et établit un premier site sur la Seine. La même année, la première grande loi sur les déchets impose pour la première fois une traçabilité des déchets considérés comme toxiques et leur applique la responsabilité élargie du producteur. Mais le modèle économique n’existe pas encore, car aucun industriel ne souhaite payer pour le traitement des déchets. C’est donc Bertrand Gontard lui-même qui convainc les agences de l’eau de financer les centres de traitement en prélevant une taxe sur les industriels, selon le principe pollueur-payeur.
Déchets dangereux : les deux pages qui écrivent le début de l'aventure
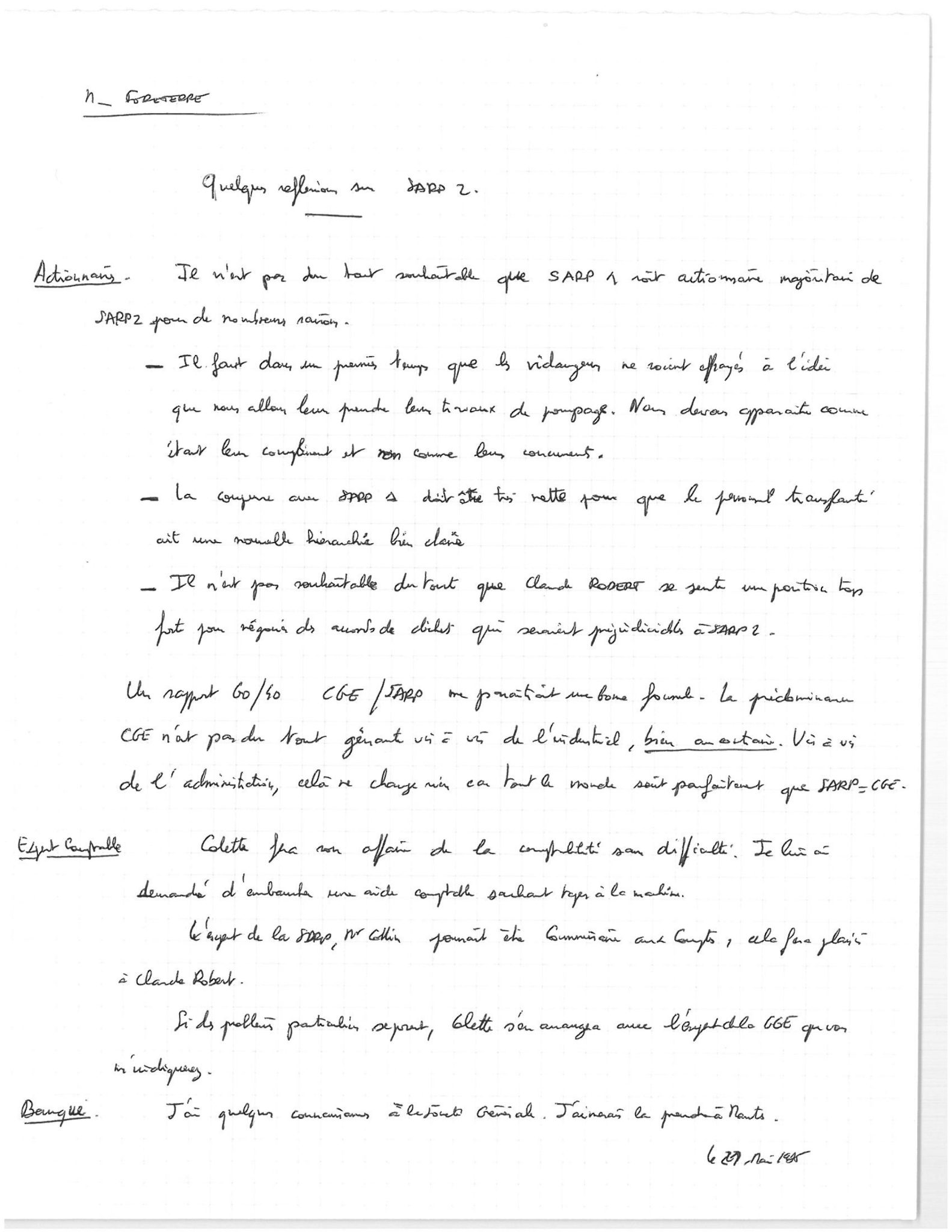
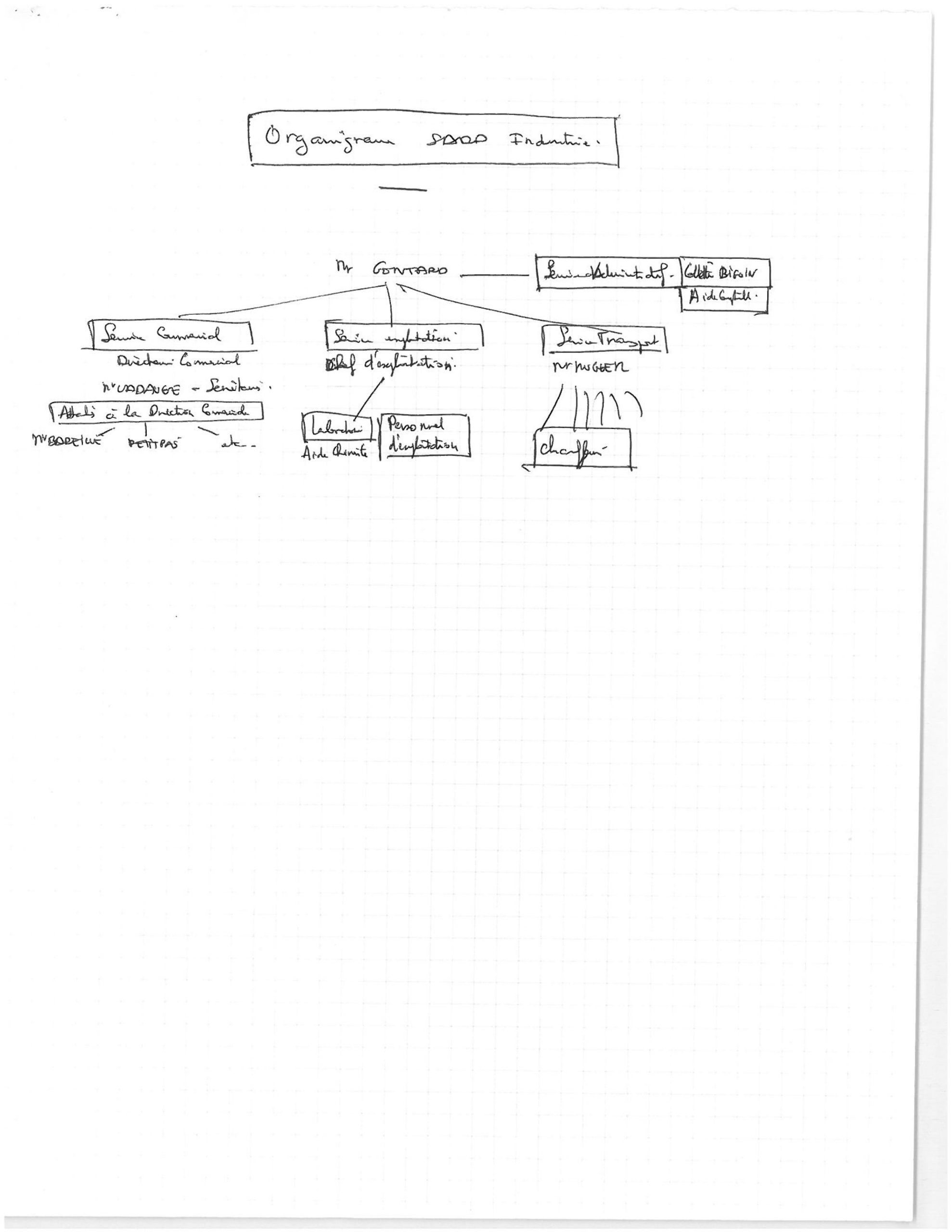
En 1975, Bertrand Gontard engage la constitution de SARP Industries en adressant un courrier à Bernard Forterre, un des principaux lieutenants du directeur général de la CGE, Guy Dejouany. L’actionnariat et le positionnement de l’activité, l’organisation comptable ( « Colette fera son affaire de la comptabilité sans difficulté » ), la création du compte bancaire et l’organigramme d’une activité appelée à faire en 2022 plus de 4 milliards d’euros de chiffre d’affaires tiennent alors en moins d’une page et demie.
Avec le même souci qu’un siècle auparavant déjà lors de l’assainissement des villes : celui de prêter attention à la réaction des vidangeurs face à ce qu’ils pourraient percevoir comme une nouvelle concurrence. Cette fois-ci, en revanche, il s’agit des vidangeurs internes à la maison. À l’époque, imaginer qu’un centre collectif de traitement ne ferait pas la collecte était une nouveauté : pour Bertrand Gontard, travailler avec tous les collecteurs, y compris les concurrents du groupe, permettait de mettre tous les efforts humains, techniques et financiers sur le traitement. Cette vision dès l’origine perdure encore aujourd’hui. Pendant très longtemps, ce fut un avantage compétitif considérable ; aujourd’hui, tout le secteur a imité ce modèle, en France et ailleurs.
À partir de l’expérience de la Compagnie Générale des Eaux dans le traitement de l’eau, mais aussi grâce à sa culture d’ingénieurs des grands corps de l’État, la SARPI expérimente, innove, et rate parfois son coup. Il faut dire qu’à l’époque les connaissances ne sont pas très développées : « Avant 1975, les déchets dangereux, notamment issus des activités industrielles et chimiques, n’étaient pas traités spécifiquement, ils finissaient en décharge ou étaient dilués dans les cours d’eau », rappelle Cédric L’Elchat, directeur général de SARP Industries. Pour traiter les déchets dangereux, elle commence par les incinérer dans un four, mais « c’est un échec retentissant », analyse Jean-François Nogrette. Le four est en effet abîmé par la corrosion engendrée par les acides libérés lors de la combustion des déchets toxiques, comme le soufre et les solvants, des produits chimiques aujourd’hui interdits. Ce n’est que partie remise, la SARPI conserve la confiance du groupe, qui lui accorde ce qui est le plus précieux dans le développement d’une activité aussi complexe : du temps.
Au bout d’environ dix ans, la filiale parvient à traiter les déchets en montant la barre des compétences de plus en plus haut, en testant et en apprenant à caractériser les déchets dangereux. « Il n’y a aucun client qui décrit vraiment comme il faut son déchet, remarque Jean-François Nogrette. Certains savent exactement d’où il vient, mais pour d’autres, c’est le résultat de mélanges. Il faut donc refaire de la chimie en laboratoire pour caractériser les déchets et éviter les mélanges dangereux. Donc nous avons développé une vraie culture de la chimie du déchet, ce qui va nous permettre un peu plus tard d’aller vers le recyclage, puisque c’est la connaissance intime du déchet qui va nous donner envie d’en extraire plus de valeur. »
Résultat de cette progression, en 2022, Veolia non seulement traite mais valorise aussi les déchets dangereux, à hauteur de 1 milliard d’euros en France et de plus de 4 milliards d’euros dans le reste du monde. Alors que SARPI traitait au départ les seuls résidus de grosses entreprises industrielles, elle est aujourd’hui sur tous les fronts, « de la chimie à la pétrochimie, à la pharmacie, aux fabricants de vaccins, en passant par les déchets d’activités de soin », précise Cédric L’Elchat. L’industrie automobile représente une branche importante des déchets dangereux, en particulier avec la multiplication des batteries au lithium pour répondre à la demande croissante en véhicules électriques. L’enjeu, en la matière, touche à leur recyclage : ces batteries en fin de vie sont à haute valeur ajoutée, au regard des différents plastiques, des solvants, des composés électroniques, et même des métaux de forte valeur comme le lithium, le cobalt, le cuivre, le manganèse ou le nickel qu’elles contiennent.
SARPI s’appuiera sur les expertises de son site en Moselle, à Dieuze, pour récupérer ces matériaux, soutenue en l’espèce par la réglementation européenne qui imposera l’inclusion des matières premières recyclées dans la production de batteries neuves : en 2031, il faudra que les batteries contiennent 16 % de cobalt recyclé, et 6 % de lithium et de nickel recyclés, des chiffres qui augmenteront au fil des années.
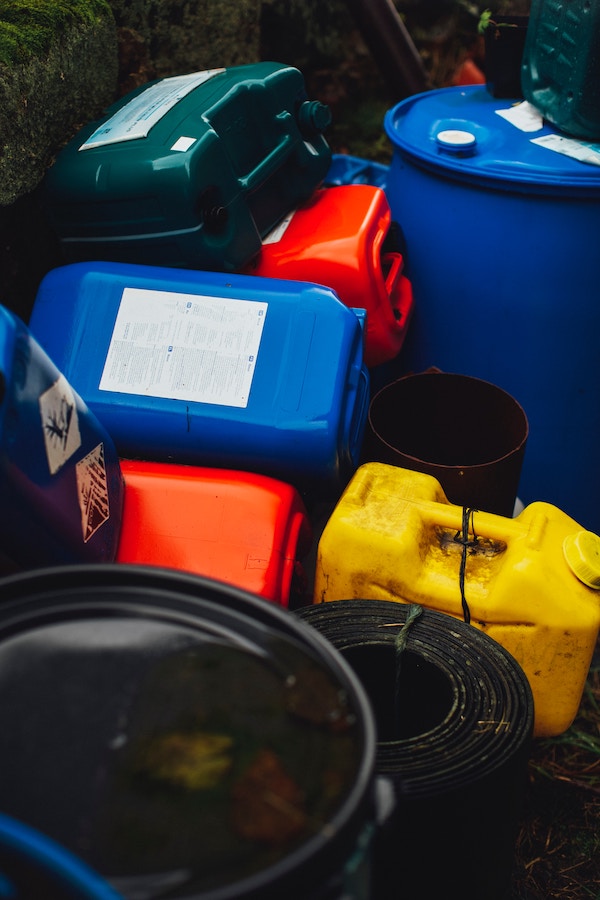
Enfin, si c’est à partir de la protection de l’eau que travaille SARPI, c’est à la protection de la terre qu’elle s’attelle aussi, en investissant le champ de la dépollution des sols. Sur des sites industriels en fin de vie, voire orphelins, « on va déployer les technologies pour traiter les friches industrielles, précise Cédric L’Elchat, traiter la dangerosité qui peut là encore affecter la nappe phréatique et les eaux de surface, pouvant être contaminées par des métaux lourds, comme le plomb ou l’arsenic, ou par des composés organiques, tels que les hydrocarbures ou le méthane ». Des solutions techniques poussées existent : la stabilisation, qui réduit la mobilité des polluants dans le sol, la solidification, qui tend à imperméabiliser le sol pour piéger les polluants, ou encore la désorption thermique, qui chauffe le sol et volatilise les composants toxiques. C’est par exemple cette dernière méthode qui a permis à Veolia d’assainir le site industriel de Fiat à Kragujevac en Serbie. À cela s’ajoutent des traitements physico-chimiques et biologiques, mais aussi… les plantes ! La phytoremédiation permet en effet de dépolluer de façon plus économique et écologique ; la technique est même expérimentée actuellement pour traiter les sols contaminés aux alentours de Fukushima.
In fine, que l’on parle de papier, de verre, de plastique, de matière organique ou de déchets dangereux, c’est, dès que l’on s’y intéresse, à la finitude des ressources que l’on est confronté. Le traitement des déchets permet de ne pas polluer celles encore disponibles à l’état naturel, quand le recyclage permet d’en limiter l’extraction. Il est en ce sens indispensable, vertueux, même, et des marges de progrès existent encore : « À Rennes métropole, abonde Martial Gabillard, il n’est plus autorisé d’amener ses tontes de pelouse en déchetterie ; cela a été remplacé par une obligation de compostage. Nous devons faire ce type de choix de société. » Mais, plus fondamentalement encore, rien ne pouvant nous permettre d’échapper aux limites naturelles, nous devons en avoir une claire conscience et poursuivre le changement des mentalités vers davantage de sobriété dans l’usage des ressources.
À Milwaukee, rien ne se perd, tout se transforme… en engrais
Au sein de la région des Grands Lacs – qui représente 20 % de l’approvisionnement mondial en eau potable et 84 % de l’eau douce de surface en Amérique du Nord – le lac Michigan est le plus grand réservoir d’eau douce des États-Unis. Le long de ses rives, la ville de Milwaukee mais aussi ses industries, qui ont historiquement servi de catalyseur à sa croissance, dépendent fortement de l’eau pour la production ou le transport. L’eau est peut-être plus encore qu’ailleurs un enjeu majeur pour la région, et de son assainissement va émerger une pépite : le Milorganite®, un engrais de haute qualité. Mais comment l’eau peut-elle bien se transformer en engrais ? Voici quelques explications…
La première station d’épuration de Milwaukee, celle de Jones Island, voit le jour en 1925. Il s’agit aux États-Unis de la première station à boues activées – un procédé biologique de traitement des eaux usées utilisant des micro-organismes. Et c’est dès 1926 que le processus de production de Milorganite® est mis en place et proposé pour fertiliser les terres agricoles de la région. Sans attendre, le marketing, la distribution et la commercialisation des engrais organiques issus de la station succèdent au traitement des eaux usées en masse : c’est une approche pionnière aux États-Unis même.
Aujourd’hui, chaque année, environ 50 000 tonnes d’engrais biosolides Milorganite® sortent de l’usine de Jones Island. Cet engrais de haute qualité a décroché le label « Exceptional Quality » de l’Agence américaine pour la protection de l’environnement (EPA). Il est également certifié par le département de l’Agriculture en raison de sa fabrication à partir de sources renouvelables. D’abord destiné aux espaces verts du territoire, le Milorganite® est aujourd’hui commercialisé à travers les États-Unis, au Canada et dans les Caraïbes.
Depuis 2008, il revient à Veolia d’exploiter la station d’épuration de Milwaukee avec une activité complète pour le compte de son client, le Milwaukee Metropolitan Sewerage District, et de son 1,1 million d’habitants : traitement et recyclage des eaux usées, production de biogaz et d’électricité, élimination et donc, bien sûr, valorisation des boues avec la production d’engrais biosolide Milorganite® (Milwaukee Organic Nitrogen). Particulièrement sensibles à la biodiversité, les collaborateurs du site ont, en marge de leur production d’engrais, construit un nichoir sur le site de production du Milorganite® pour accueillir des faucons pèlerins. Alors que ses populations avaient très fortement diminué après la Seconde Guerre mondiale, elles sont à nouveau en expansion depuis leur protection dans les années 1970. Tout un symbole de la capacité des hommes à agir pour protéger l’environnement.
En Australie, l’engrais est dans le lac salé
Les engrais alternatifs aux engrais de synthèse peuvent venir du recyclage des déchets organiques… ou être puisés directement dans un lac. C’est le cas en Australie-Occidentale, où la puissance des rayons du soleil permet d’extraire du sulfate de potassium (SOP), un engrais essentiel à la nutrition des plantes, à partir du Lake Way, très riche en minéraux. Cela ne va pas néanmoins sans un besoin de maîtrise technologique avancée : la toute première usine de traitement du pays, mise en service par Salt Lake Potash Limited (ou SO4), s’est dotée d’une technologie de cristallisation développée par Veolia.
Le Lake Way est un aquifère de saumure peu profond, sous une surface sèche de lac salé. Depuis des millions d’années, les minéraux extraits du bassin-versant du lac s’y écoulent. D’où sa richesse particulière en potassium, l’un des trois nutriments essentiels à la croissance des plantes, prête à être exploitée. « Le principal avantage du sulfate de potassium est qu’il ne contient pas de chlorure, souligne Tony Swiericzuk, l’ancien directeur général de SO4. Le terme “potasse” fait généralement référence au chlorure de potassium, engrais de référence pour la fertilisation, mais mal toléré par les sols pauvres et arides d’Australie, de Méditerranée, d’Afrique et du Moyen-Orient.
Tout comme par certaines cultures de rente – fruits, baies, noix et agrumes –, car il affecte le goût et la couleur. »
Après avoir extrait la saumure, éliminé les sels contaminants et laissé l’eau s’évaporer grâce à l’action du soleil, la concentration en sulfate de potassium augmente progressivement, avant de passer à l’étape de cristallisation. « Pour convertir les sels récoltés en sulfate de potassium de qualité supérieure, Veolia a conçu deux cristalliseurs. Un pour cultiver et purifier les cristaux de sulfate de potassium, un autre pour produire des sels de schoenite secondaires, récupérés à partir de l’eau-mère de sulfate de potassium recyclée. Ces sels sont ensuite combinés aux sels de schoenite primaires et ajoutés au cristalliseur de SOP pour maximiser le rendement en potassium », indique Jim Brown, ancien vice-président exécutif de Veolia Water Technologies Americas.
L’objectif est de livrer 245 000 tonnes de sulfate de potassium par an en production régulière. Un complément bienvenu pour l’Australie, qui importe la quasi-totalité de son SOP par bateau de Belgique et d’Allemagne, et une nouvelle source qui joue la proximité, donnée importante pour les clients d’Asie du Sud-Est et d’Australie.
- INA Société. Vie moderne : les ordures [vidéo en ligne]. YouTube, 23 juillet 2012. ↩︎
- INA Société. Ibid. ↩︎
- INA Société. Ibid. ↩︎
- OCDE, communiqué de presse, « Selon l’OCDE, les déchets plastiques produits au niveau planétaire devraient presque tripler d’ici 2060 », 3 juin 2022. ↩︎
- Mandard, Stéphane, “Le plastique, une menace protéiforme [Plastic, a protean threat]”, Le Monde, May 29, 2023 ↩︎