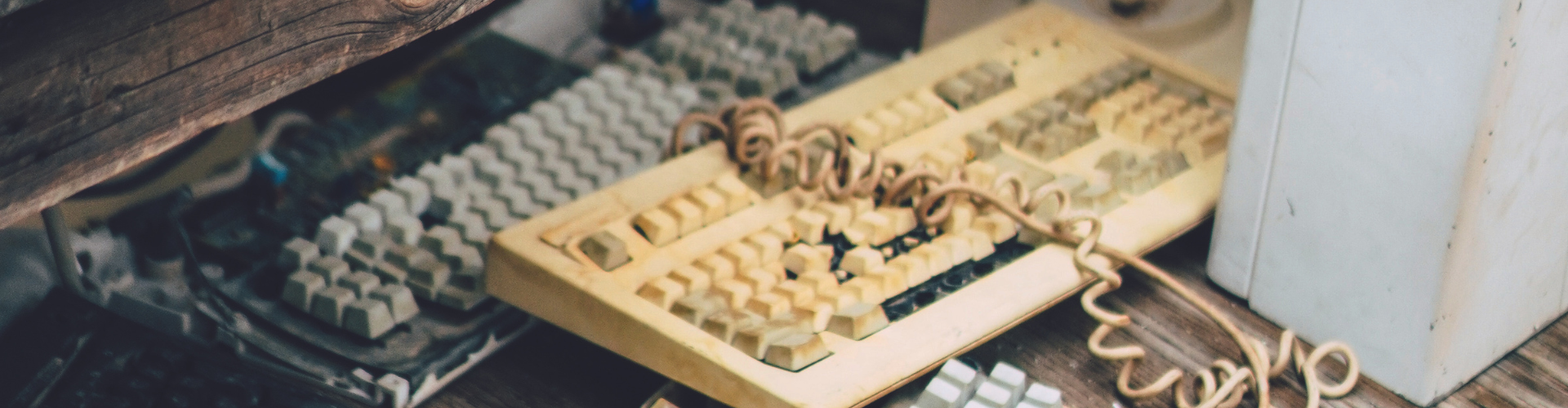
Recycling Waste: Between Fundamental Rediscoveries and a New Industrial Epic
The gap between the rapid technical invention of solutions for valorization and the slow adoption of new sorting practices prompts us to return to the historical roots of recycling. On one hand, today's circular economy has nothing to do with waste-free organic societies, as current valorization relies entirely on the production of waste, (i.e., discarded material, detached from the person who produced it and who no longer wants to see it). Therefore, it is necessary to raise awareness among users who have become insensitive to this invisible part of themselves. It would be more effective to work upstream so that no one can say of any material, “This is no longer me.” International comparisons show that waste valorization can paradoxically be easier to implement in emerging countries where waste has always been a resource for the local populations living around and on landfill sites.
On the other hand, it is essential not to forget that the transposition of Antoine Lavoisier and Jean-Antoine Chaptal's organic chemistry expertise into the industrial and judicial realms resulted in the idea that waste is nothing more than a residue waiting to be chemically valorized. This neutralized all fights against pollution in the nineteenth century. The growth of the new recycling market today requires a contract of trust that clears up ambiguities and invents a new metabolism that cannot be a reactivation of an idealized past.
Grégory Quenet
Modern recycling, as we understand it today, gradually emerged in the twentieth century, particularly in the second half of the century. In Great Britain, the verb “to recycle” has been in use since 1926, and the term “recycling” appears shortly after World War II. In France, the term recyclage first appeared in 1960—but it wasn't until the 1970s that these words became commonly used in everyday language, coinciding with the explosion of waste production. In 1970, graphic designer Gary Anderson created the iconic universal recycling logo based on the Möbius strip—which has only one surface and one edge—as part of a competition launched during the first Earth Day celebrated in Wisconsin. Originally intended for recycled paper products, the symbol later became widespread, used for all recycled or recyclable products worldwide. If the symbol is unaccompanied by any additional information, it indicates that the product is simply recyclable, while the appearance of a percentage signifies the proportion of recycled materials present. Its graphic simplicity is key to its success, allowing it to be adapted to all contexts and countries, to the extent that Gary Anderson realized the importance of his design when he spotted it on a trash can in Amsterdam a few years later!
The first to recycle material from waste after 1945 were the cardboard manufacturers, papermakers, and glassmakers, who were heirs to the old ragpickers. At that time, the Soulier Company, which would later become part of CGEA and Veolia, abandoned its declining ragpicking activities to focus on paper recycling by partnering with Cartonneries La Rochette. To supply its factories, the Soulier Company collected paper from shopping centers, supermarkets, and even schools after raising awareness of its collection among schoolchildren. After the 1973 oil crisis, glassmakers encouraged the French to recycle their glass bottles, as recycled glass required less energy. This was the first time such a recycling system was established for household waste. In 1976, an agreement was signed between the glass industry—represented by the Chambre syndicale des verreries mécaniques de France—and the Ministry of Industry and Research.
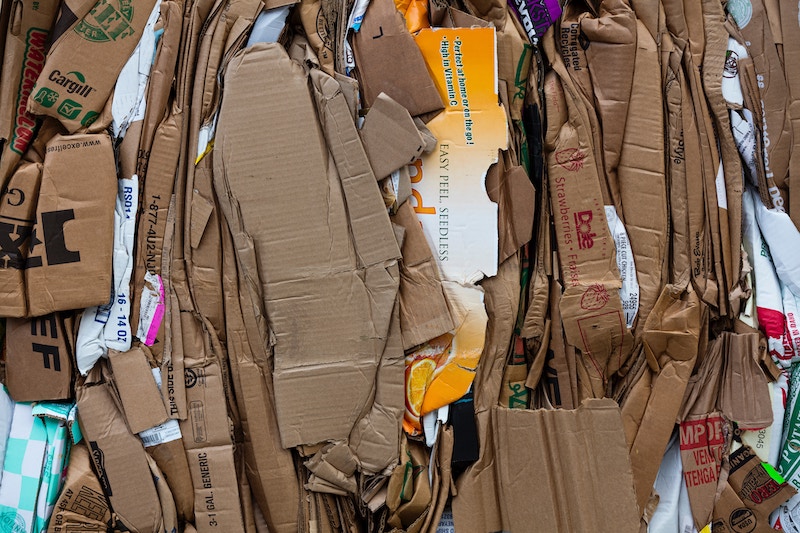
However, these initiatives still occupied a relatively small place compared to the explosion of what a 1972 television report called “lost packaging,”1, i.e., non-returnable packaging. This accounted for 5 percent of packaging in 1960, 30 percent in 1972, and the journalist mentioned projections of 80 percent by 1980. From 220 kilograms of waste per year per person in the 1960s, France rose to 360 kilograms in 1990. Faced with this trend, recycling efforts remained localized for a long time. It was only in the 1980s that things began to scale up in a very pragmatic way. “We were then able to establish supply chains,” noted Martial Gabillard, Director of Resource Recovery at Veolia. “We identified sources, such as recycling wood, plaster, and even plastic. Our Waste Management division increasingly focused on sorting. If we saw that there was wood in the region, we would have a container for it. In recycling centers, we set up bins for green waste and, if necessary, for cardboard and scrap metal, which were used by cardboard manufacturers and scrap dealers. But it wasn't until the 1992 law that these flows were orchestrated.”
Reflecting the spirit of the times and the simultaneous undertaking of other countries, the French Royal Law revamped the country's policy on household waste management. In addition to encouraging a reduction in landfilling and energy production from incineration, it advocated for waste reduction and valorization, driving the development of new facilities such as sorting centers and recycling centers. Like Germany from 1989 onwards, it further expanded the producer's responsibility, defined by the “polluter-pays” principle in the 1975 European directive, to household waste. It also fostered the creation of eco-organizations—federations of producers who assumed responsibility for the end-of-life management of their products.
“In the 1990s, local authorities no longer had the financial and technical means to manage waste, which was becoming more complex,” explains Helen Micheaux, Associate Professor of Management Sciences at AgroParisTech. “Another solution had to be found. It was in this context that the idea of producer responsibility emerged.” “There was a real awareness. All these waste materials that we handled could be recycled. To achieve this, they had to be removed from household bins, implementing specific recycling channels for sorting and preparing them for reintegration,” says Françoise Weber, Director of Extended Producer Responsibility Schemes in France at Veolia. “With eco-organizations, we started sorting plastic, cardboard, paper, and glass packaging.” In the early 1990s, it was time to accelerate recycling efforts.
Plastic Is No Longer Fantastic, Especially When It Comes to Single-Use
Plastic, it must be said, has taken a central position in the world of packaging and waste. Regardless of the oil shocks, plastic waste has increased from 4 percent of household waste in France in 1973 to 11.2 percent fifty years later. The pursuit of simplicity and convenience dominated an era waiting for a complete liberation from physical constraints, even though the seeds of the problems it caused were present from the beginning. In a 1972 television report archived by INA, the director of a plastic packaging company extolled the virtues of his industry: “We have always thrown away packaging; remember the tin cans, the drums? The normal trend is to seek lightweight packaging that is not returnable, and plastic materials are ideal for this.”2
Plastic was fantastic, to the extent that a Belgian artist adopted the stage name Plastic Bertrand, in reference to the plastic garments worn by “punks,” a movement that advocated for a break from the previous generation. At the same time, downstream in the production and consumption system, the director of an incineration plant, a certain Mr. Fourment, began to lament the proliferation of plastic bottles in waste: “These bottles are indestructible, which is why, to some extent, when we talk about biodegradability, from our current state of knowledge, it's science fiction.”3
Jean Soulier, Advocate of Waste Recovery and Social Entrepreneur
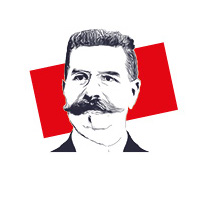
Born in 1868 in Meulan-en-Yvelines, Jean Soulier's journey is intertwined with the historical contingencies of the first half of the twentieth century. After studying at Lakanal High School in Paris, he joined the family waste recovery and valorization business to gain experience. However, his marriage to Emma Vachon led him to work with his father-in-law in Rouen. It is in this city that Établissements Soulier, master ragpickers, saw a significant part of its paper and textile recycling activity thrive on an industrial scale, even though the company remained relatively small.
In the 1910s, Jean traveled to the United States and Russia, which helped him build a network of contacts in the export industry that would serve him throughout his life. Unlike those waste collection companies that manage public services, the Soulier family directly profited from their trade: they purchased waste, sorted, valorized, and resold it at higher prices, generating revenue through the margins they obtained from these operations. Consequently, their success depended on the supply and demand of their products, and they only established themselves in regions where they believed there was a market.
In this context, the outbreak of World War I in 1914 temporarily halted their growth. For instance, a factory in Aisne was destroyed. In 1919, the family decided to reorganize the business, which refocused its operations in Rouen and transformed into the Société Anonyme des Anciens Établissements Soulier. Each brother focused on a specific activity: Jean became a wholesale rag dealer, and Eugène became a dealer in hides, leather, and horns. As the third administrator, Georges, Jean's son, was responsible for the recovery and shredding of rags and trimmings for paper mills. Their stores began to open throughout the city and its surroundings, and a large warehouse was established. Additionally, the family purchased real estate to accommodate workers who came to work, sometimes seasonally, in their factories.
The 1920s represented the golden age of the Établissements Soulier. With their growth, they acquired a large plot of land in Plaine Saint-Denis, a region of Paris already populated by many wholesale rag dealers. They established a branch there, which allowed them to expand their operations in Paris dealing in hides and leather, which they sold to shoe manufacturers in the capital and its suburbs. They subsequently acquired a business in Paris and workshops in Montreuil for the hides division.
At that time, Soulier surpassed all other rag establishments in Paris, leading them to go public in 1924. Although the rag trade had faced complications in large cities since the introduction of garbage trucks that operated early in the morning, in small towns and villages, it was still possible to collect from individuals who were happy to sell their rags, rabbit skins, animal bones, or anything they had scavenged from illegal dumps. Despite being a notable figure in the city of Paris, a member of the general council since 1901, and although he resided there part of the year at 115 Boulevard Haussmann, Jean Soulier remained loyal to Rouen. As a radical-socialist, he also sought to improve working conditions in the recovery and sorting trades. He built housing for seasonal workers in his factories, promoted apprenticeships, established a mutual aid fund for the profession, and attempted to maintain year-round production to “avoid unemployment among staff.” From 1921 to 1923, he oversaw the modernization of the old establishments in Plaine Saint-Denis, with special consideration for female workers, including a cafeteria, changing rooms, sinks, and showers.
Before the stock market crash of 1929, Jean Soulier embarked on another trip to the United States, continuing his efforts to expand exports. However, the global economic crisis quickly dashed his hopes.
In June 1930, Jean Soulier admitted that the company was facing a real setback, with merchandise dropping from 25,000 tons to 16,544 tons. The establishment turned to selling real estate to survive. Despite his social aspirations, Jean Soulier struggled to implement the social laws of the Popular Front in 1936, including paid vacations and a forty-hour workweek, which further destabilized an already fragile economic model. During World War II, he lost close collaborators, including his own son Georges. His workshops in Rouen were bombed. Établissements Soulier partnered with Cartonneries de la Rochette to create the Société Nouvelle des Établissements Soulier in 1946, a final attempt to overcome the crisis in rag, paper, and leather recovery, but the figures still did not improve. Ill and weakened, Jean Soulier delegated some of his responsibilities and passed away in 1954 in Rouen, where his company continued to collect and export rags as best it could. The establishments bearing his name were absorbed by the paper group Cartonneries de la Rochette in 1960, which, in turn, sold them to Compagnie Générale des Eaux in 1990 as part of consolidating various waste management services. While this recycling activity remained fragile, it allowed the group to develop expertise in the field.
In Chennai, the Informal Sector: A Key Link in Recycling
With a population of 1.4 billion, India has become a true demographic powerhouse, surpassing China. Alongside rapid urbanization and increased access to mass consumption, the subcontinent faces significant challenges in waste management. Historically, there have always been what are known as “informal waste pickers,” and they still play a crucial role that needs to be taken into account by major companies like Veolia.
Indian cities produce 68.8 million tons of waste per year, a quantity that could increase by 133 percent between 2015 and 2041—a staggering figure, especially considering that 91 percent of the collected waste is not valorized and ends up in open dumpsites.
In India, post-consumer waste is sometimes managed by the informal sector, where men and women provide pre-collection and valorization services. According to a document from the Centraider network, “these operators are often difficult to know and identify, as they make themselves less visible to avoid humiliation from the population or interventions from the authorities.”
This is why municipalities and even companies struggle to collaborate with informal sector workers. However, the stakes are significant, as highlighted by Kabadiwalla Connect, a technology-based social enterprise based in Chennai: “Leveraging the informal ecosystem of urban waste recyclers could reduce the amount of waste sent to landfills in Indian cities by 70 percent.”
Ragpickers, recyclers, and waste collectors often work in precarious conditions, but they play an essential role in waste management, helping to reduce the quantity of waste and minimize its environmental impact. In 2015, in the city of Chennai, Kabadiwalla Connect mapped and documented for the first time the “waste entrepreneur” or kabadiwalla in India. The study identified nearly two thousand of them in Chennai alone, where they collect over 24 percent of total recyclable waste, including paper, metal, plastic, and glass.
However, these actors face various challenges, including lack of visibility, incomplete information, and lack of official integration into the system. To address these issues, Kabadiwalla Connect has developed a platform to facilitate interaction between companies like Veolia and the informal sector. “Our goal is to strengthen the value of the informal supply chain,” explains Siddharth Hande, the founder and CEO of Kabadiwalla Connect. “One of our main initiatives is the establishment of a highly optimized plastic recovery facility supplied by the informal sector. We have a year and a half of experience with PET (petroleum-sourced plastic), and we achieve a high level of quality: 80 to 90 percent of PET is recovered on average, thanks to good sorting. The partnership with Veolia helps us improve the transformation and high-end valorization process.”
The company has set up a specific recycling infrastructure to obtain recyclable materials from the informal sector, initially focusing on plastic. The objective is to demonstrate that it is possible to obtain a significant volume of waste from the informal sector while benefiting from better prices, improved collection schedules, and a better understanding of the recycling market.
Gradually, the importance of managing the environmental impacts of this new material is emerging. It is in Germany and the Scandinavian countries that selective sorting has been most quickly embraced by the population in order to achieve this. Marc-Olivier Houel, General Manager of Recycling and Waste Valorization in France, as well as former Industrial Waste and Household Waste Manager in Sarre, remembers a time when everything had to be invented: “The Germans were pioneers in eco-packaging and the creation of eco-organizations,” he says. “In September 1990, they established the first eco-organization in Europe—the Dual System Deutschland (DSD)—and the Green Dot (Der Grüne Punkt)—the circular logo representing two intertwined arrows indicating that the company contributes to the treatment of packaging, which was later adopted by many countries, including France.
Veolia, which has just entered the German market through the acquisition of the cross-border company Kléber, will play a central support role by advising cities on the implementation of the new regulations, distributing new transparent yellow bags, raising awareness among citizens through collection operators, and recruiting specific sorting ambassadors.” Gradually, waste such as bottles, plastic films, yogurt pots, Tetra Pak packaging, and aluminum cans are collected and given back to the DSD: in the Saarland region, the quantities of lightweight household packaging collected and sorted have increased from zero in 1992, when the first selective collection system was implemented, to thirty kilograms per capita per year in 1995.
However, in Germany itself, sorting alone did not immediately lead to recycling. The created plastic streams did not immediately find outlets that had not previously existed; instead, they led to the creation of these outlets, starting from the late 1990s. “It was like a startup,” recalls Marc-Olivier Houel. “We were transforming our environment, and that of our clients, by putting pressure on the reuse of materials.” The creation of a material resource allowed for the establishment of dedicated plastic recycling channels for horticultural pots or the automotive industry five to six years later. In 1998, Mercedes signed a framework agreement for collection from car dealerships and the recycling of damaged car parts (bumpers, glass, batteries, wipers, etc.). “We found recycling channels with Mercedes throughout Europe,” recalls Marc-Olivier Houel. “The system was almost a closed loop. This is how we played a leading role in promoting the circular economy in Germany and Europe.”
To expand these channels, partnerships with large companies are essential for exploring possibilities and finding new outlets for recycled plastic, which historically had been used mainly for non-technical applications such as recycled PVC pipes. This entails both “assisting industrial companies in changing their approach to raw materials, accepting small defects in recycled plastics,” explains Martial Gabillard, “and adapting to the most complex demands of companies that want to maintain high-quality products with specific technical specifications”. Over the past twenty years, progress has been significant, to the point where, in 2021, the technological leader Thales partnered with Veolia to create the first eco-designed SIM card made from recycled plastic that meets the necessary requirements for strength, flexibility, and heat resistance.
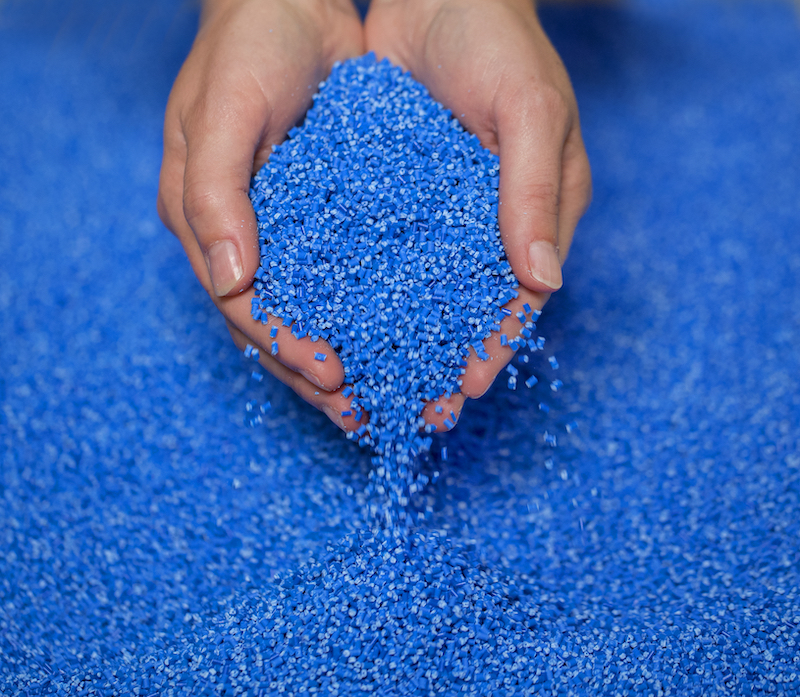
© Veolia Media Library - Christophe Majani D’Inguimbert
In general, "there is a great deal of partnership work with eco-organizations. We need to work together to secure long-term material resources for innovative recycling industries," says Françoise Weber and Sophie Petibon, Commercial Director of Recycling and Waste Valorization at Veolia. This partnership also extends to eco-design in order to close the loops. Veolia encourages its partners to manufacture monoplastic products that are pure and simple, requiring fewer chemicals and less energy for recycling. “We offer consulting services on eco-design to industrial companies, as well as certification of the level of recyclability of their packaging," explains Sven Saura, Director of the Recycling and Plastics division at Veolia. "It should be noted that using a bottle made from recycled plastic emits 75 percent less CO2 than one made from virgin plastic, and eco-design can further reduce this.”
Simplifying and standardizing the plastics used, especially those derived from recycling, is key to promoting the development of a circular economy. This is why Veolia formalized its brand of circular polymers, PlastiLoop, in 2022. With PlastiLoop, the group offers a range of recycled products structured to meet the needs of various industries that want to reduce their use of virgin plastic. It is an offer tailored to the specific needs of each industry, from automotive to agri-food, aiming to establish recycling as a shared standard.
However, the challenge of plastic use and recycling is far from being solved. The world consumes over 350 million tons of plastic each year, and according to the United Nations Environment Programme, if nothing is done, this consumption figure could triple by 2060 and exceed one billion tons.4 Currently, only 9 percent of plastic is recycled worldwide, almost 50 percent is landfilled, 19 percent is incinerated, and the rest ends up polluting the environment, sometimes in the form of micro- or nanoplastics. As an article in Le Monde published in 2023 states, “Every minute, the equivalent of a garbage truck filled with plastic waste is dumped into the oceans"5. While technical solutions are being developed, regulations still have a role to play, as is often seen in the interaction between technology and the law. Mandatory incorporation of recycled plastic in products, such as the European Union's requirement for bottlers to incorporate at least 25 percent of recycled plastic into their bottles by 2025 and 30 percent by 2030, will be crucial.
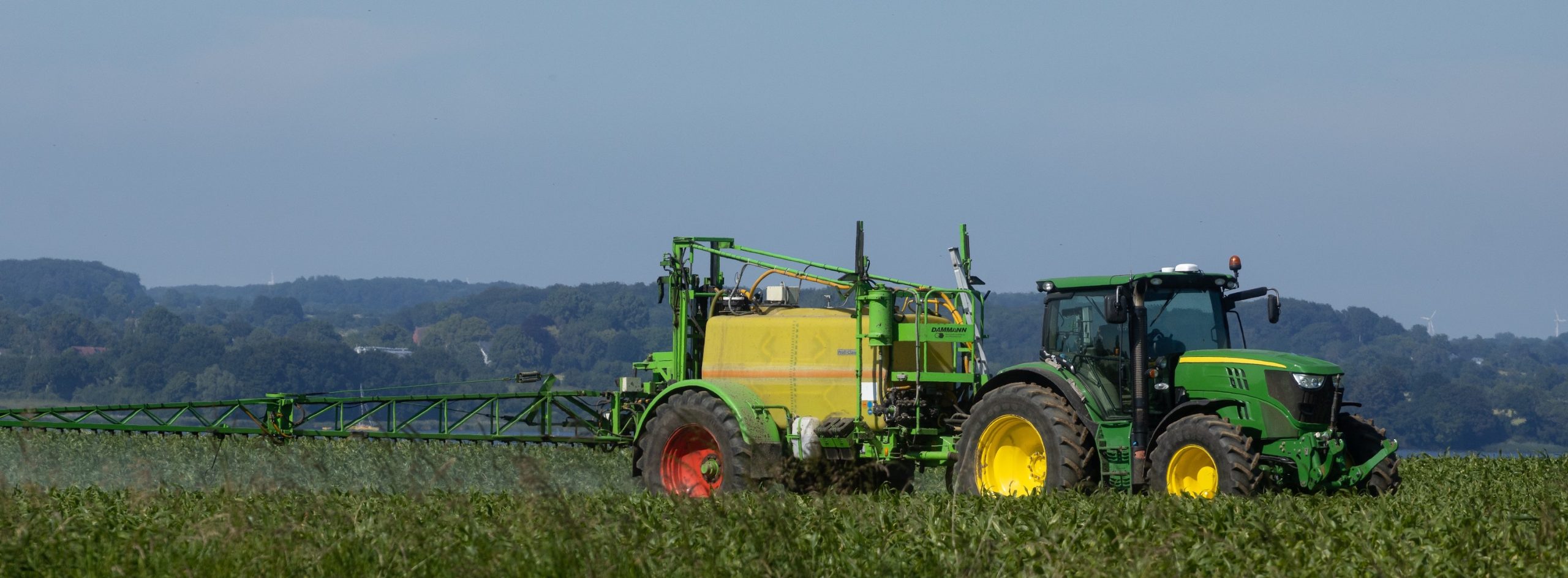
Organic Valorization: From Agricultural Fertilizers to Animal Nutrition
Organic materials have historically been among the most valued waste, even before the advent of sanitary cities. Derived from urban sludge and emptied septic tanks, they were transformed through industrial processes into fertilizers or compost before the establishment of sewer networks, which made the sludge too liquid to be spread in fields, and the mass disposal of household waste, which gradually mixed and compacted the waste in garbage trucks, making their valorization nearly impossible.
Organic Fertilizers Back in Favor
With the resurgence of organic fertilizers in the twentieth and twenty-first centuries, the emergence of wastewater treatment plants, and the new distinction of waste streams, the recycling of organic matter regained precision, as seen in Milwaukee in 1926. Veolia mobilizes its sewage sludge for this purpose and, in line with evolving regulations and needs, has established logistics that now allow for organic waste’s return to the land. Biodegradable waste collected directly from the agri-food industry, large retailers, or restaurants is transported to composting units before being spread in fields. Composting is the key method for valorizing this waste. It is a controlled biological process of degrading organic materials such as food waste, garden residues, and agricultural by-products. This ancient technique transforms the waste into compost, an organic amendment rich in nutrients that can be used as fertilizer to enrich agricultural soils as well as private gardens. Veolia has worked to optimize these processes and, most importantly, to operate them in accordance with the strict sanitary and environmental conditions defined by a series of laws and directives that consider the diversity of pollutants to be treated before returning waste to the soil.
The resurgence of organic valorization is more than a return to common sense. In the era of climate change, it is a means of capturing carbon in soil. “Biowaste allows us both to nourish plants with nitrogen- and phosphorus-rich fertilizers and to enrich soils with carbon,” emphasizes Maelenn Poitrenaud, Innovation and Development Manager at Sede within Veolia, the entity dedicated to agricultural services in France. According to the Four per One Thousand Initiative, launched by the French Minister of Agriculture Stéphane Le Foll during the COP21 in Paris in 2015, an annual increase of 0.4 percent in carbon stocks sequestered in the soil could limit the concentration of CO2 from human activities in the atmosphere. This represents significant potential, considering that in France alone, Sede composts 800,000 tonnes annually from its sixty composting sites. Moreover, in a nutrient-rich soil, plants grow faster and capture more carbon through photosynthesis. Hence, the importance of a mass return to organic valorization.
In France, the valorization of biowaste has progressed thanks to strict regulations promoting its sorting, separate collection, and appropriate treatment. Since January 1, 2012, large biowaste producers have been required to implement sorting and valorization solutions for these types of waste. Over the years, the AGEC (Anti-Waste for a Circular Economy) law has lowered the threshold so that by 2024, all producers will be subject to this obligation. Consequently, local authorities will have to provide individuals with separate collection and valorization solutions, notably through individual and collective composting. This challenge is significant, considering that currently half of France’s biowaste ends up in the gray bin (destined for incineration), and only 30 percent of the population reports sorting their biowaste at the source. Solutions exist, but they need to be generalized and provided with the means for deployment, both in France and worldwide, in order to increase their value.
The Development of Higher Value-Added Valorization
In contrast to the indiscriminate massing of waste streams, it is their increasingly minute separation that enriches the value of recycled organic matter. Veolia, in partnership with Angibaud and Recyfish, markets fertilizers made from fish waste. Primarily used in high-value crops such as viticulture and market gardening, the resulting “fish guano” is an organic fertilizer rich in nitrogen and phosphorus that also affects the microfauna and microflora of the soil, crucial for the optimal exchange of elements between the soil and the plant.
Moving upmarket also requires mastery of new techniques. “Since its creation in 1979, Sede has acquired more expertise in sludge, drying, composting, and anaerobic digestion, enabling us to offer a more diverse range of biowaste valorization pathways today,” explains Morgane Maurin, Secretary-General of Sede. “What we spread in the fields is a very diverse range, including high-quality compost and premium fertilizers such as Pro-Grow, Vital, and ADS.” On Veolia's composting sites, as Guillaume Wallaert, former Director of Biowaste Solutions at Veolia, points out, “the AEROcontrol system, for example, accelerates the degradation of residues by using a probe to measure parameters such as compost temperature to optimize air injection, improve the maturation process, and obtain higher-quality compost.”
To better support farmers, Veolia has also pioneered innovations in precision agriculture. During spreading, it is also possible to observe how plants consume fertilizer and what their needs are, in order to optimize its use. “We apply biostimulants to the plant so that it can use the fertilizer to its maximum potential, allowing it to develop optimally and resist its environment,” says Maelenn Poitrenaud. The same goes for soils: the Soil Advisor application helps farmers optimize fertilization by using organic fertilizers such as compost.
Veolia now even goes so far as to be a shareholder of Mutatec, a startup that transforms organic waste into proteins for animal nutrition through the breeding of black soldier flies, which produce insect protein concentrates from the waste material. “Bioconversion is a future activity that addresses the global food challenge and the objective of a circular economy by providing a better path for the valorization of organic by-products,” emphasizes Jean-Christophe Perot, regional director for the Southeast region at Sede.
From Pollution Control to Valorization: The Emblematic Example of Hazardous Waste
The progress of recycling over the past few decades has been achieved through both the rediscovery of ancient practices and the implementation of new responsibilities, the development of new techniques, and the strengthening of environmental standards. The different material flows have thus seen an improvement in their valorization, but perhaps none is as emblematic of the era and the DNA of Veolia as hazardous waste. Constituting a new and complex pollution, the treatment and recycling of these waste streams have developed from the entrepreneurial spirit of Veolia's teams. Jean-François Nogrette, director of the France zone and Special Waste Europe, is well acquainted with this story. “It was Veolia's Water branch that invented what became hazardous waste treatment in order to preserve its resource,” he summarizes. It all began when Bertrand Gontard, director of the water treatment plant in Méry-sur-Oise, realized that industrial effluents discharged into the Oise River were threatening the treatment of its water. To purify the river’s water, he had to use even more activated carbon, and a shortage was looming, which would mean cutting off drinking water for the residents. To address the problem, he proposed that industrial companies treat their effluents directly in a specialized center, without waiting for the pollution to reach the river.
“In his career, he also encountered a company called SARP,” recalls Jean-François Nogrette, “which occasionally collected and pumped hazardous waste. He drew inspiration from this to create SARP Industries in 1975, a subsidiary of Compagnie Générale des Eaux,” and established a first site on the Seine. That same year, the first major waste law imposed for the first time traceability of waste considered toxic and applied the principle of extended producer responsibility. However, the economic model did not yet exist, as no industrial company wanted to pay for waste treatment. Therefore, it was Bertrand Gontard himself who convinced water agencies to finance treatment centers by levying a tax on industrial companies, according to the polluter-pays principle.
Déchets dangereux : les deux pages qui écrivent le début de l'aventure
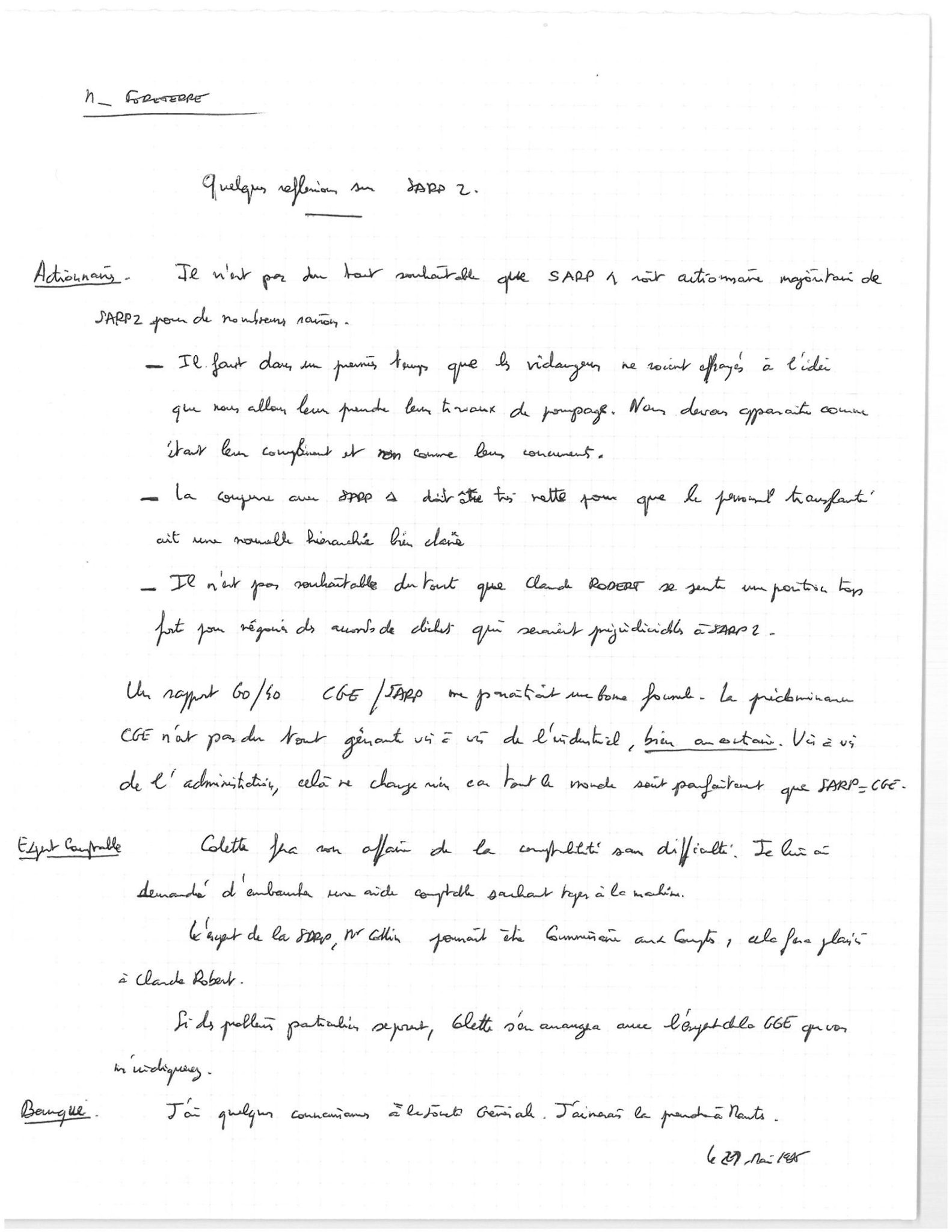
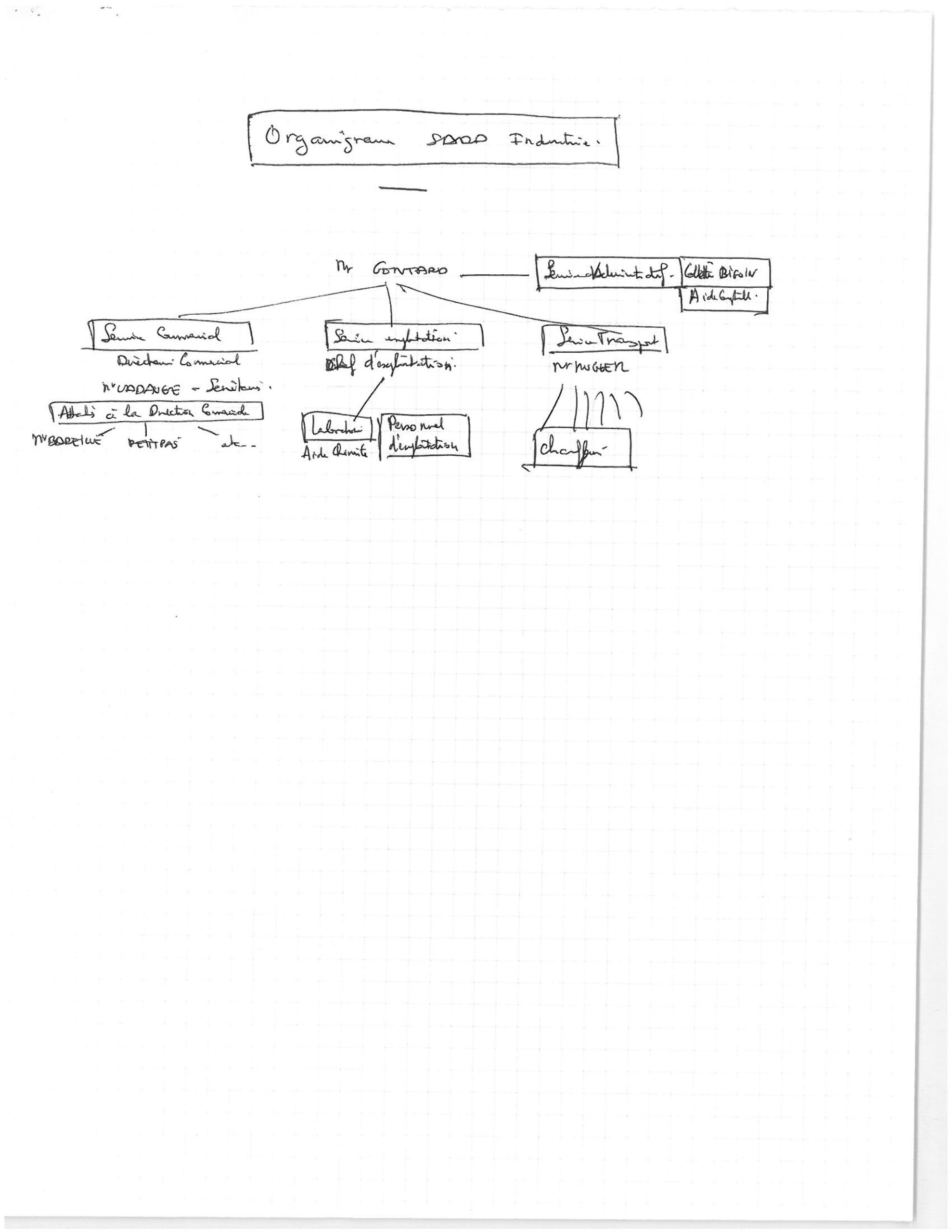
In 1975, Bertrand Gontard initiated the establishment of SARP Industries by sending a letter to Bernard Forterre, one of the key lieutenants of Guy Dejouany, the CEO of CGE. The ownership structure and positioning of the business, the accounting organization (“Colette will take care of the accounting without difficulty”), the creation of a bank account, and the organizational chart of an activity expected to generate over four billion euros in revenue in 2022 were summarized in less than one and a half pages.
Similar to a century earlier during the sanitation of cities, the attention was given to the reaction of vacuum truck operators who might perceive it as new competition. However, this time it was the internal vacuum truck operators within the company. At that time, the idea that a collective treatment center would not handle collection was a novelty. For Bertrand Gontard, working with all collectors, including the group's competitors, allowed for all human, technical, and financial efforts to be focused on treatment. This vision from the very beginning still persists today. For a long time, it was a significant competitive advantage. Nowadays, the entire sector has adopted this model, both in France and elsewhere.
Based on the experience of the Compagnie Générale des Eaux in water treatment and its culture of engineers from prestigious government bodies, SARPI (SARP Industries) experimented, innovated, and sometimes faced failure. It should be noted that at that time, knowledge in this field was not well-developed. “Before 1975, hazardous waste, particularly from industrial and chemical activities, was not specially treated; it ended up in landfills or was diluted in watercourses,” recalls Cédric L'Elchat, CEO of SARP Industries. Initially, SARPI attempted to incinerate hazardous waste in a furnace, but this was a resounding failure: the furnace was damaged by corrosion caused by acids released during the combustion of toxic wastes such as sulfur and solvents, which are now prohibited chemicals. However, SARPI retained the trust of the group, which provided it with the most valuable resource for developing such a complex activity: time.
After approximately ten years, the subsidiary managed to treat the waste by continuously raising the bar of expertise, testing, and learning to characterize hazardous waste. “There is no client who accurately describes their waste,” notes Jean-François Nogrette. “Some know exactly where it comes from, but for others, it is the result of mixtures. We have to perform chemical analysis in the laboratory to characterize the waste and prevent dangerous combinations. Thus, we have developed a genuine culture of waste chemistry, which later motivated us to move toward recycling it, as it is this intimate knowledge of the waste that drives us to extract more value from it.”
As a result of this progress, in 2022, Veolia not only treats but also valorizes hazardous waste, generating over one billion euros in revenue in France and over four billion euros worldwide. While SARPI initially treated waste from large industrial companies, it is now active in various sectors, including “chemistry, petrochemistry, pharmaceuticals, vaccine manufacturers, and healthcare waste,” as specified by Cédric L'Elchat. The automotive industry represents a significant branch of hazardous waste, particularly with the proliferation of lithium batteries to meet the growing demand for electric vehicles. The challenge in this area lies in their recycling, as end-of-life batteries contain valuable materials such as various plastics, solvents, electronic components, and even high-value metals like lithium, cobalt, copper, manganese, or nickel.
SARPI will leverage the expertise of its site in Dieuze, Moselle, to recover these materials, supported by European regulations that will require the inclusion of recycled raw materials in the production of new batteries. By 2031, batteries will need to contain 16 percent recycled cobalt and 6 percent recycled lithium and nickel, with these percentages increasing over the years.
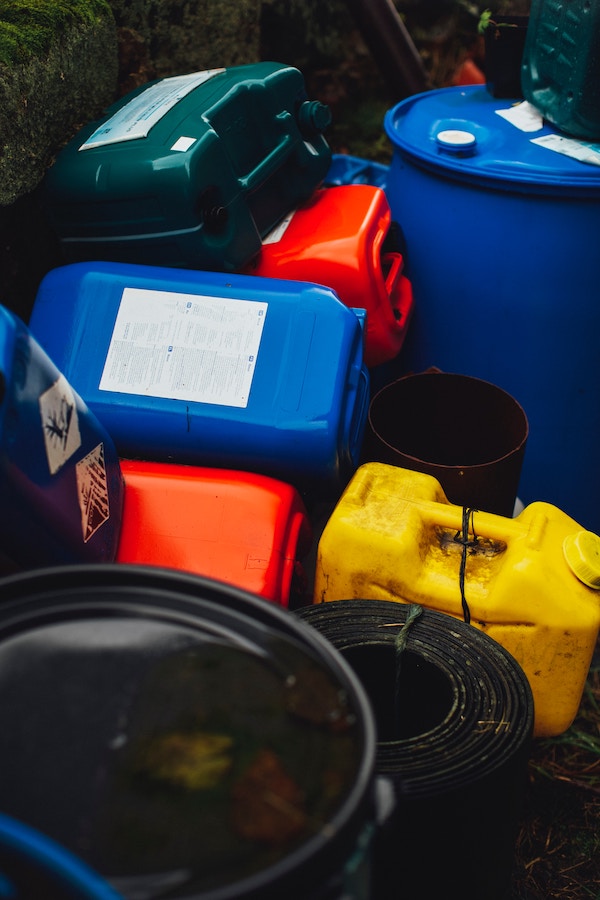
Finally, while SARPI initially focused on water protection, it also addresses soil decontamination, investing in the remediation of industrial sites that are either at the end of their life or abandoned. “We deploy technologies to treat industrial brownfields,” explains Cédric L'Elchat. “We treat the hazards that can affect groundwater and surface waters, which may become contaminated by heavy metals such as lead or arsenic or by organic compounds such as hydrocarbons or methane.” Advanced technical solutions exist, including stabilization to reduce the mobility of pollutants in the soil, solidification to make the soil impermeable and trap pollutants, and thermal desorption to heat the soil and volatilize toxic components. For example, the latter method was used by Veolia to remediate the Fiat industrial site in Kragujevac, Serbia. Physico-chemical and biological treatments are also used, along with phytoremediation, which offers a more economical and ecological approach to soil decontamination. This technique is currently being used experimentally to treat contaminated soils around the Fukushima power plant in Japan.
Ultimately, whether it is paper, glass, plastic, organic matter, or hazardous waste, when we consider these materials, we are confronted with the finiteness of our resources. Waste treatment prevents pollution of the remaining natural resources, while recycling helps reduce extraction. It is essential and even virtuous in this sense, and there is still room for improvement. “In the Rennes metropolitan region, for example,” adds Martial Gabillard, “you are no longer allowed to bring grass clippings to waste disposal facilities; instead, composting is mandatory. We need to make these kinds of societal choices.” However, more fundamentally, since we cannot escape natural limits, we must remain aware and continue to steer mindsets toward greater resource efficiency.
In Milwaukee, Nothing Is Wasted, Everything Is Transformed... into Fertilizer
Within the Great Lakes region—which represents 20 percent of the world's fresh water supply and 84 percent of North America's surface fresh water—Lake Michigan is the largest reservoir of fresh water in the United States. Along its shores, the city of Milwaukee and its industries, which have historically served as catalysts for its growth, depend heavily on water for production or transportation. Water is perhaps even more of a major issue for the region than elsewhere, and from its purification emerges a gem: Milorganite®, a high-quality fertilizer. But how can water be transformed into fertilizer? Here are some explanations.
The first wastewater treatment plant in Milwaukee, Jones Island, was established in 1925. It was the first activated sludge plant in the United States—a biological process for wastewater treatment using microorganisms. And it was as early as 1926 that the Milorganite® production process was implemented and offered to fertilize the agricultural land in the region. Without delay, marketing, distribution, and commercialization of organic fertilizers derived from the plant followed the mass treatment of wastewater: it was a pioneering approach in the United States.
Today, approximately fifty thousand tons of Milorganite® biosolid fertilizer are produced annually at the Jones Island factory. This high-quality fertilizer has earned the “Exceptional Quality” label from the US Environmental Protection Agency (EPA). It is also certified by the Department of Agriculture due to its production from renewable sources. Initially intended for green spaces in the area, Milorganite® is now marketed throughout the United States, Canada, and the Caribbean.
Since 2008, Veolia has been responsible for operating the Milwaukee wastewater treatment plant with comprehensive activities on behalf of its client, the Milwaukee Metropolitan Sewerage District, and its 1.1 million inhabitants: wastewater treatment and recycling, biogas and electricity production, disposal, and, of course, the valorization of sludge with the production of Milorganite® biosolid fertilizer (Milwaukee Organic Nitrogen). Sensitized to biodiversity, the site's employees have even built a nest box on the Milorganite® production site to accommodate peregrine falcons. While this species’ population had greatly declined after World War II, they have been expanding again since their protection in the 1970s—a symbol of humans’ ability to act to protect the environment.
In Australia, Fertilizer Comes from the Salt Lake
Alternatives to synthetic fertilizers can come from recycling organic waste...or be extracted directly from a lake. This is the case in Western Australia, where the power of sunlight allows for the extraction of potassium sulfate (SOP), an essential fertilizer for plant nutrition, from Lake Way, which is rich in minerals. However, this requires advanced technological expertise: the country's first processing plant, operated by Salt Lake Potash Limited (SO4), has adopted crystallization technology developed by Veolia.
Lake Way is a shallow brine aquifer beneath a dry salt lake surface. Minerals that have been extracted from the lake's catchment area have been flowing into it for millions of years, resulting in its particularly rich concentrations of potassium, one of the three essential nutrients for plant growth, ready to be exploited. “The main advantage of potassium sulfate is that it does not contain chloride,” emphasizes Tony Swiericzuk, former CEO of SO4. “The term ‘potash’ usually refers to potassium chloride, the benchmark for such fertilizers, but it is not well-tolerated by the poor, arid soils of Australia, the Mediterranean, Africa, and the Middle East.”
“It also affects the taste and color of certain cash crops such as nuts, berries, citrus, and other fruits.”
After extracting the brine, removing contaminating salts, and allowing the water to evaporate through the action of the sun, the concentration of potassium sulfate gradually increases before entering the crystallization stage. “To convert the collected salts into high-quality potassium sulfate, Veolia has designed two crystallizers. One is used to grow and purify potassium sulfate crystals, and the other is used to produce secondary schoenite salts, which are recovered from the recycled potassium sulfate mother liquor. These salts are then combined with primary schoenite salts and added to the SOP crystallizer to maximize potassium yield,” explains Jim Brown, former Executive Vice President of Veolia Water Technologies Americas.
The goal is to deliver 245,000 tons of potassium sulfate per year in regular production. This is a welcome addition for Australia, which imports almost all of its SOP by ship from Belgium and Germany, and it provides a new source that offers proximity, which is important for customers in Southeast Asia and Australia.
- INA Société. “Vie moderne : les ordures” [online video]. YouTube, July 23, 2012. ↩︎
- Ibid. ↩︎
- Ibid. ↩︎
- OECD, press release, “Global plastic waste set to almost triple by 2060, says OECD,” June 3rd, 2022. ↩︎
- MANDARD, Stéphane. “Le plastique, une menace protéiforme [Plastic, a protean threat],” Le Monde, May 29, 2023. ↩︎